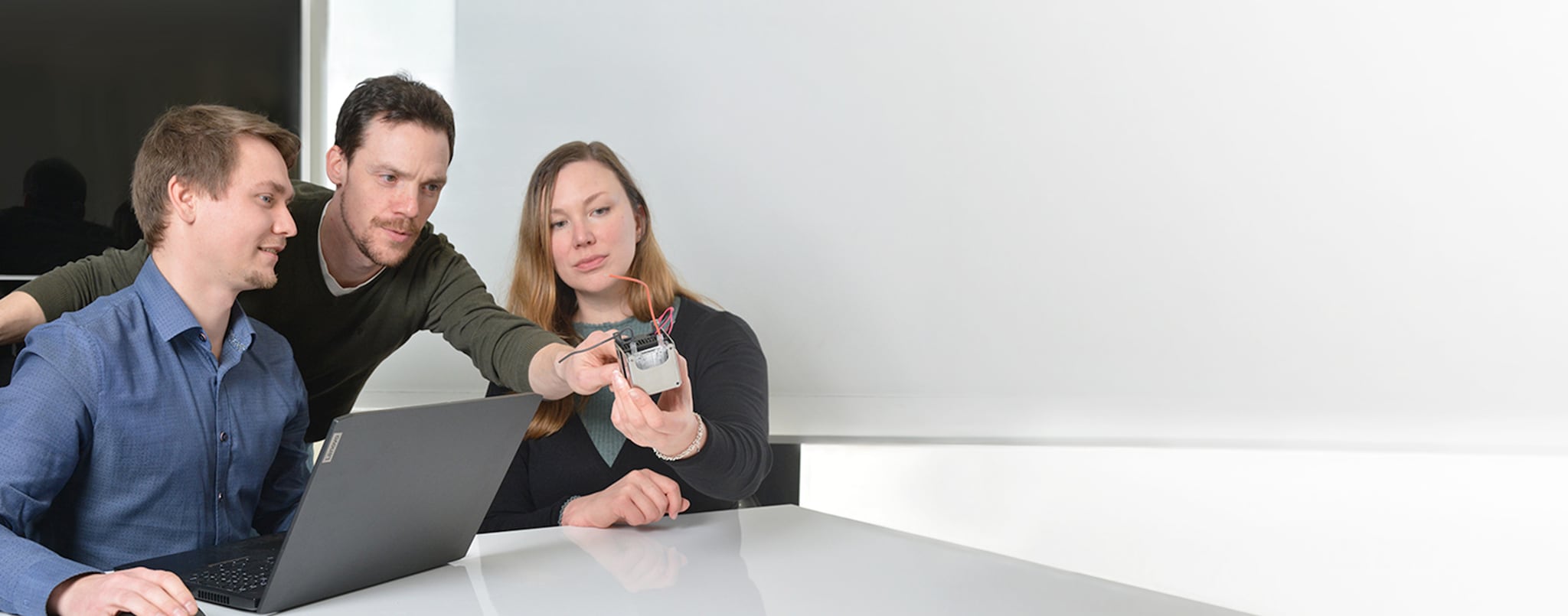
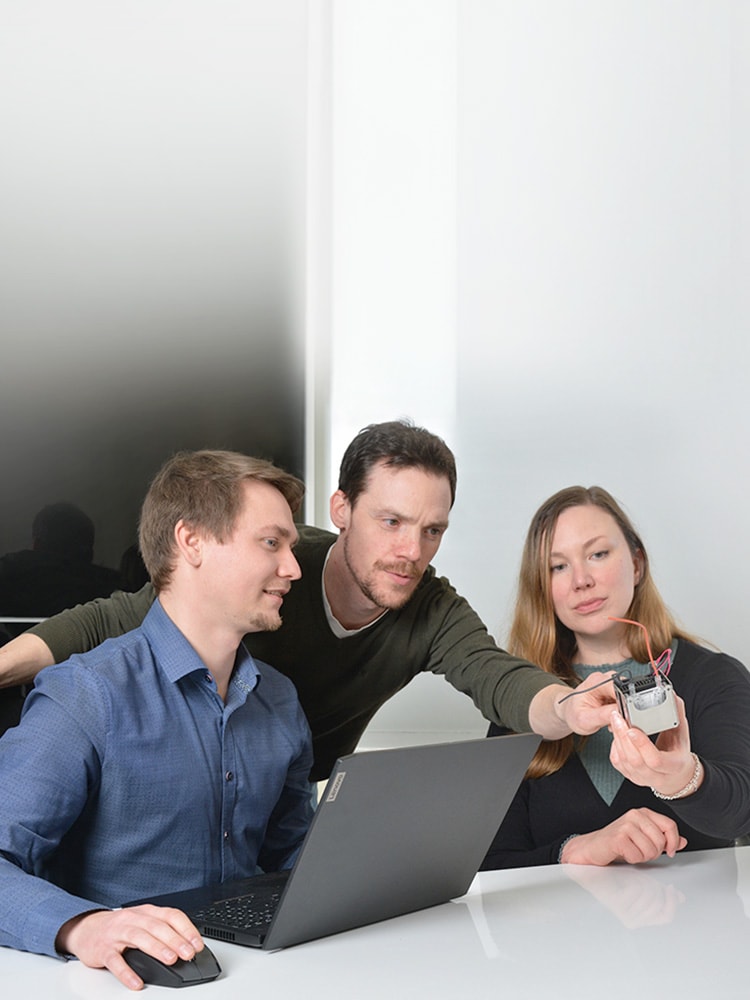
Making Low-Temperature Sterilization of Medical Devices Standard Practice: The Aspirations of relyon plasma’s Team
In medical environments, it is imperative to maintain instruments in a constantly clean state to prevent infections and ensure safety. Yet, as medical equipment becomes increasingly sophisticated, including the emergence of delicate electronic devices, there is a growing demand for sterilization and disinfection methods that don’t compromise these devices. Developed by relyon plasma, a TDK Group company, MediPlas utilizes oxygen and nitrogen in the air to generate, on the spot, reactive oxygen and nitrogen species (RONS) like nitrogen oxides and hydrogen peroxide as well as ozone to disinfect medical equipment safely and efficiently. Learn how relyon plasma’s team is undertaking the challenges of creating groundbreaking devices that will enable the low-temperature sterilization of medical equipment.
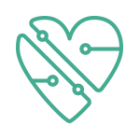
Disinfection and sterilization are paramount in healthcare settings
Outbreaks of infectious diseases have reinforced our understanding that disinfecting our hands in daily life helps mitigate their spread. The significance is even more pronounced in healthcare settings like hospitals. According to a report released by the World Health Organization (WHO) in 2022, out of every one hundred patients admitted to urgent care facilities, seven in high-income countries and fifteen in low- to middle-income countries develop healthcare-associated infections (HAIs) during their stay, with an average of one in ten patients succumbing to infection-related complications. (Source: WHO launches first ever global report on infection prevention and control, WHO)
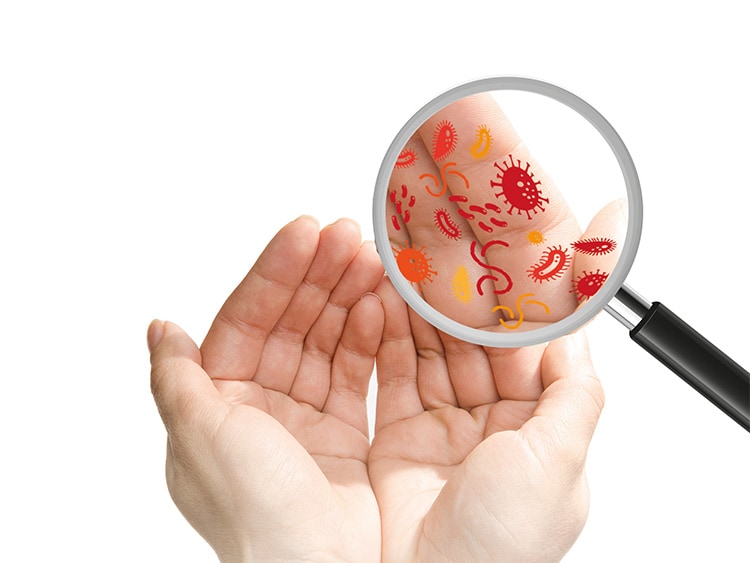
At healthcare facilities, sterilization and disinfection of examination instruments, surgical tools, and medical equipment are rigorously implemented to prevent the spread of viruses and bacteria among patients, physicians, and nurses. Particularly with medical equipment that comes into direct contact with patients, stringent measures are taken to virtually eliminate microbes. These methods employ high-pressure steam, chemicals, and gases, and the technologies in this field have continually evolved over time.
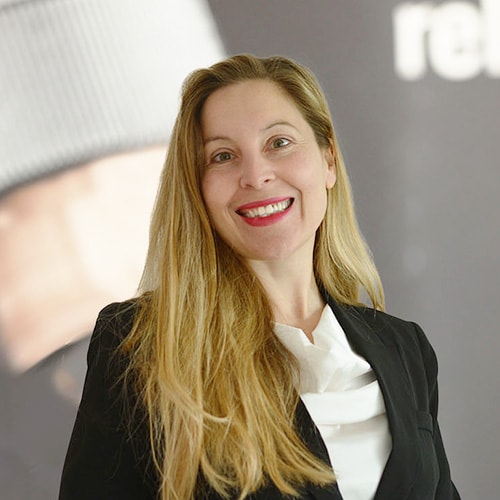
Head of Sales and Marketing
relyon plasma GmbH
Simona Lerach, responsible for sales and marketing of MediPlas at relyon plasma, described the voices being heard at the forefront of healthcare. “In the medical field, there is a growing demand for sterilizing and disinfecting instruments more safely and cost-effectively. The development of MediPlas was sparked by healthcare professionals’ needs for customizable, time-saving, sustainable product solutions that could reliably replace conventional sterilization processes. We deeply believed from the beginning that our expertise in low-temperature plasma technology can bring unprecedented sterilization and disinfection devices to reality.”
Disinfection and sterilization methods
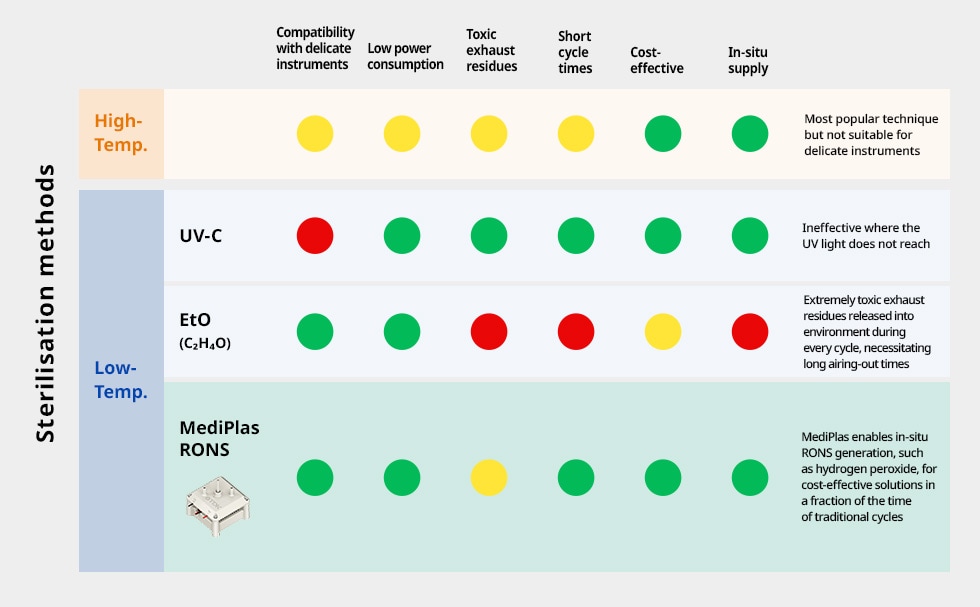
The most common technique for sterilizing medical instruments today involves high-pressure steam. Instruments are placed in an autoclave and subjected to high-pressure and high-temperature steam (over +120°C) to kill any microbes. The process has been widely adopted because of its safety due to the absence of toxic chemicals and its effectiveness even in short cycles.
The growing need for low-temperature sterilization at the forefront of healthcare
As medical technologies advance, the range of medical equipment continues to diversify. Among them are precision instruments and certain plastics that cannot withstand high temperatures. For the sterilization and disinfection of delicate, thermally vulnerable equipment, methods employing ethylene oxide (EtO) gas have been commonly used. In this method, the gas is injected into a sealed container and does not entail high temperatures, accommodating a broad range of equipment. However, ethylene oxide is highly toxic, necessitating protective gear like masks and goggles for operators as well as time-consuming gas removal procedures known as aeration.
Jose dos Santos, who handles product marketing at TDK Group company TDK Electronics, explained the risks. “The principal drawback of EtO is that it is a hazardous, toxic gas that can harm both humans and the environment. Exposure to high levels of EtO can cause serious health problems, including respiratory issues, skin irritation, and nerve damage.
Moreover, the sterilization process can take several hours to days—a massive disadvantage in healthcare settings where time is of the essence.”
Examples of electronic equipment in clinical settings
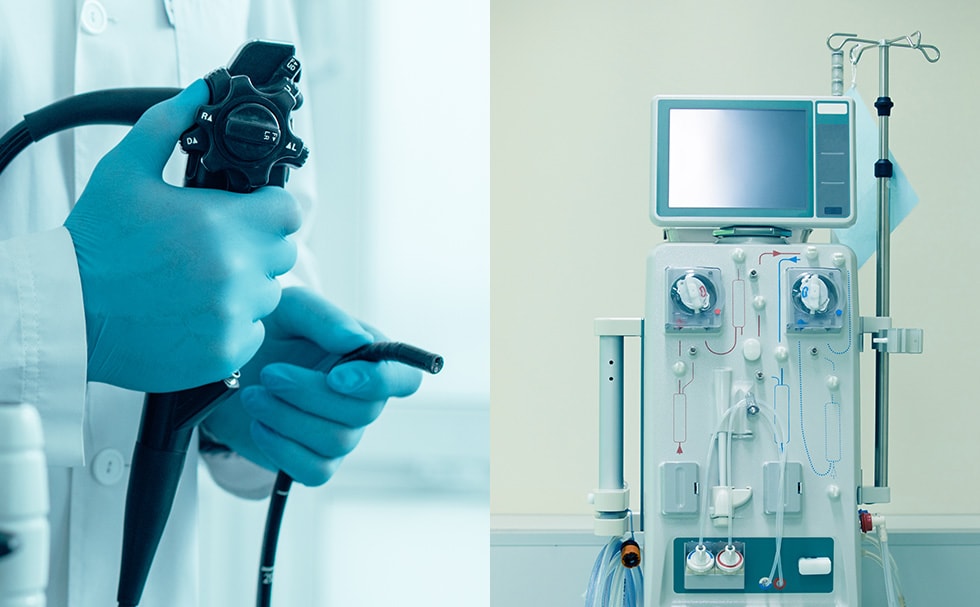
The potential of low-temperature sterilization using plasma
Amid the demand for safe and cost-effective sterilization and disinfection methods, attention is turning to reactive oxygen and nitrogen species (RONS) like nitrogen oxides and hydrogen peroxide as promising alternatives to ethylene oxide. Notably, they possess potent antioxidant properties and the ability to sterilize effectively without leaving toxic residues.
Drawing on years of experience in the application of atmospheric plasma and expertise in multilayer ceramic technologies, relyon plasma has developed compact plasma generators using piezoelectric transformers and successfully established them on the market. Building on this, the MediPlas plasma system suitable for medical technology applications was developed. A system that generates hydrogen peroxide and other sterilizing gases and can be safely integrated into medical devices.
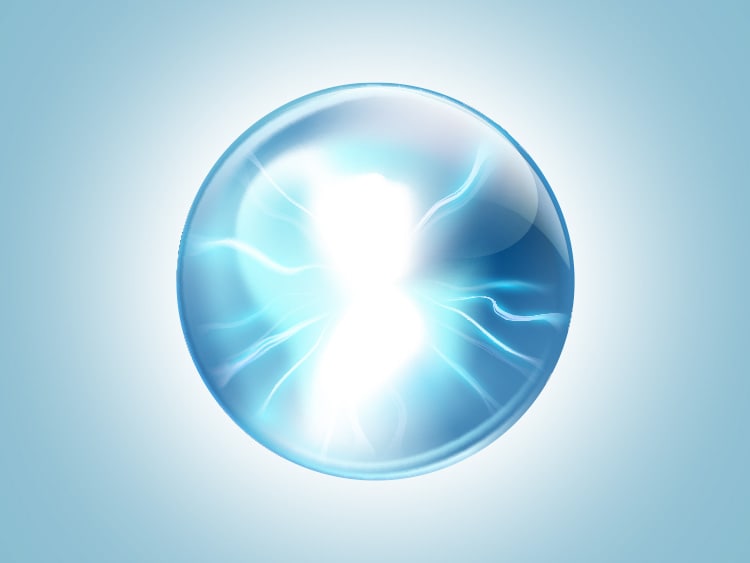
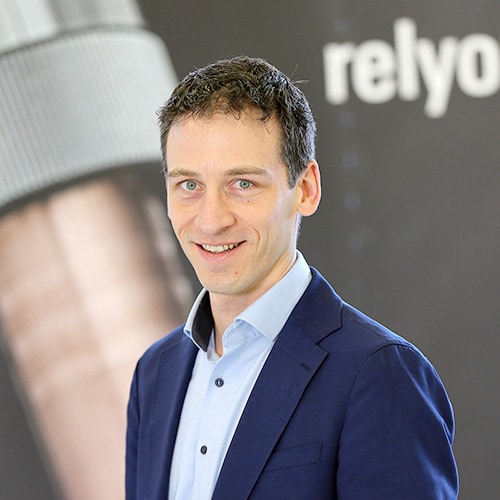
Head of R & D
relyon plasma GmbH
Florian Freund, who led the development of MediPlas at relyon plasma, shared his insights. “Drawing on our many years of experience in the field of plasma technology, we were able to solve the typical challenges that arise during development right from the start. In particular, the materials used must meet high requirements, which we tackled with a network of highly specialized manufacturers of modern plastics and experts in sealing technology. Our deep, foundational know-how on plasma-specific high-voltage generation enabled the compact and robust design of the electronics.”
How MediPlas works
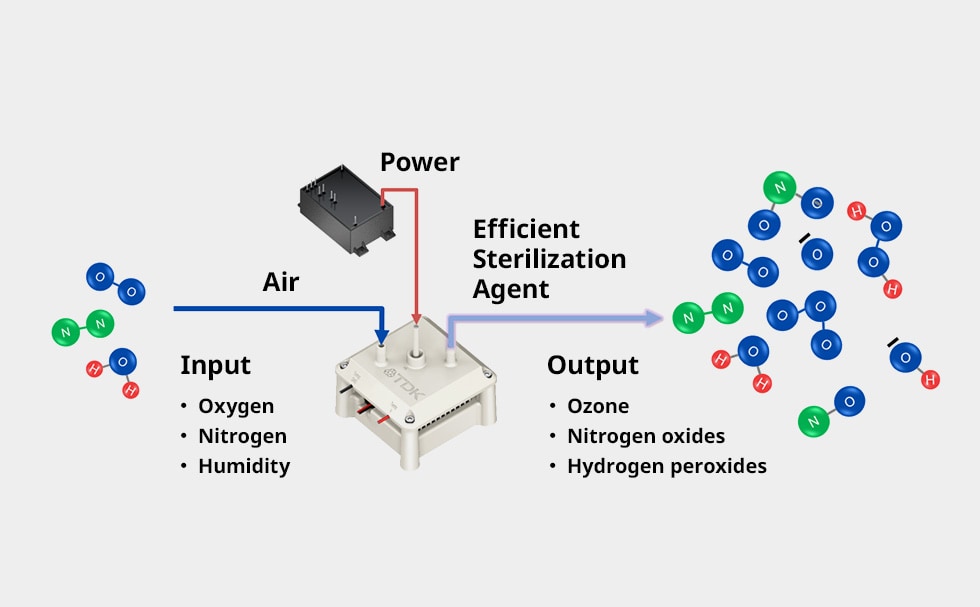
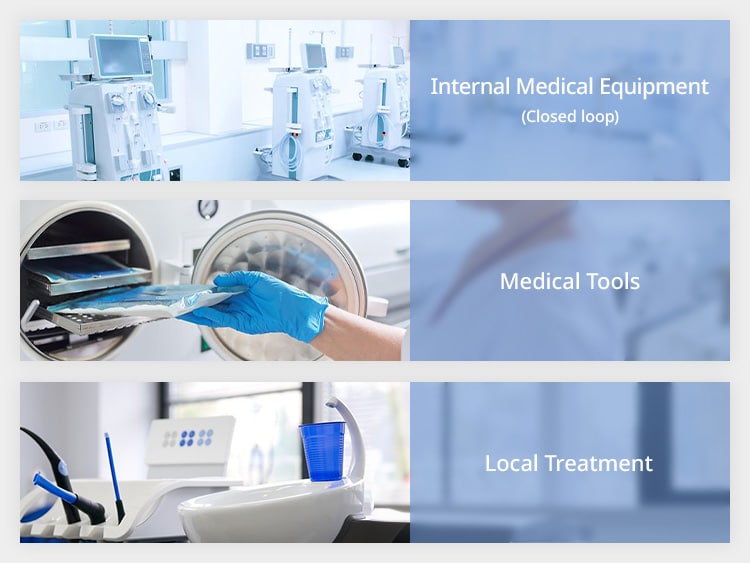
Thanks to its compact size, MediPlas can be integrated into a variety of devices for internal reprocessing. It can be also used in combination with chamber systems to disinfect various suitable medical devices such as periodontal and dental instruments, as well as entire components.
Freund elaborated on the potential of MediPlas. “Compact, safe, and energy-efficient, MediPlas holds immense versatility and limitless possibilities. While our primary focus is on healthcare, we envision extending our solutions to the industrial domain in the future. Examples include optimizing seed disinfection and germination time in agriculture and extending product shelf lives in the food industry. MediPlas can also find applications in water treatment and beyond, which speaks to its multifaceted potential. Our objective is to collaborate with customers to find optimal solutions. We look forward to helping address their challenges by leveraging our expertise effectively.”
relyon plasma team members and headquarters
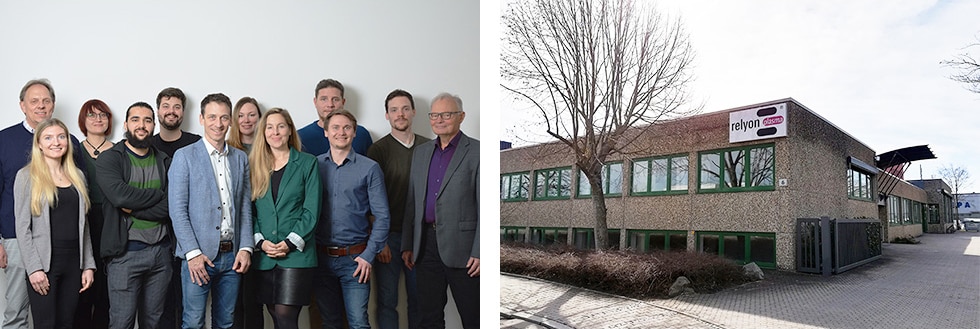
MediPlas Reactor and Driver
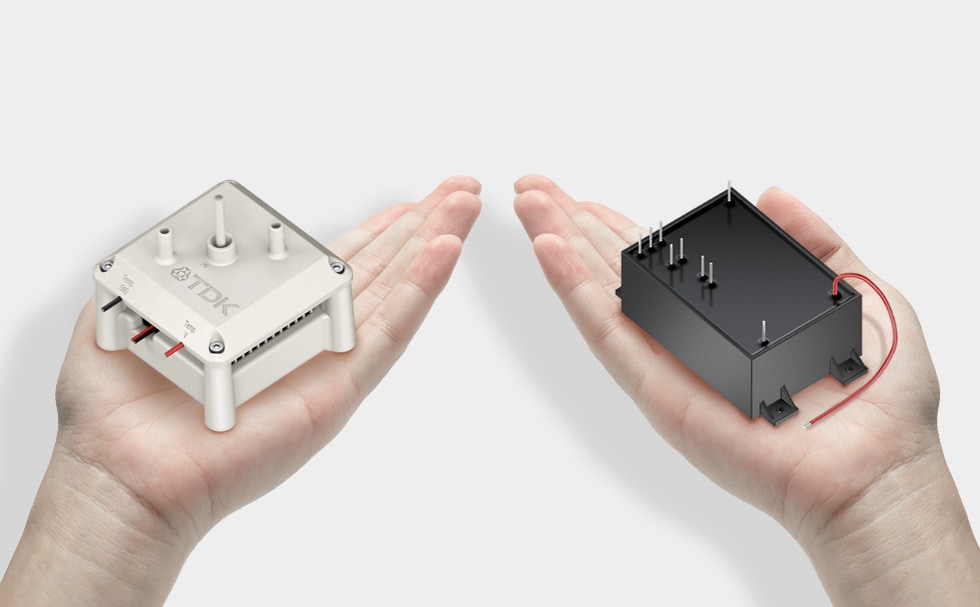
