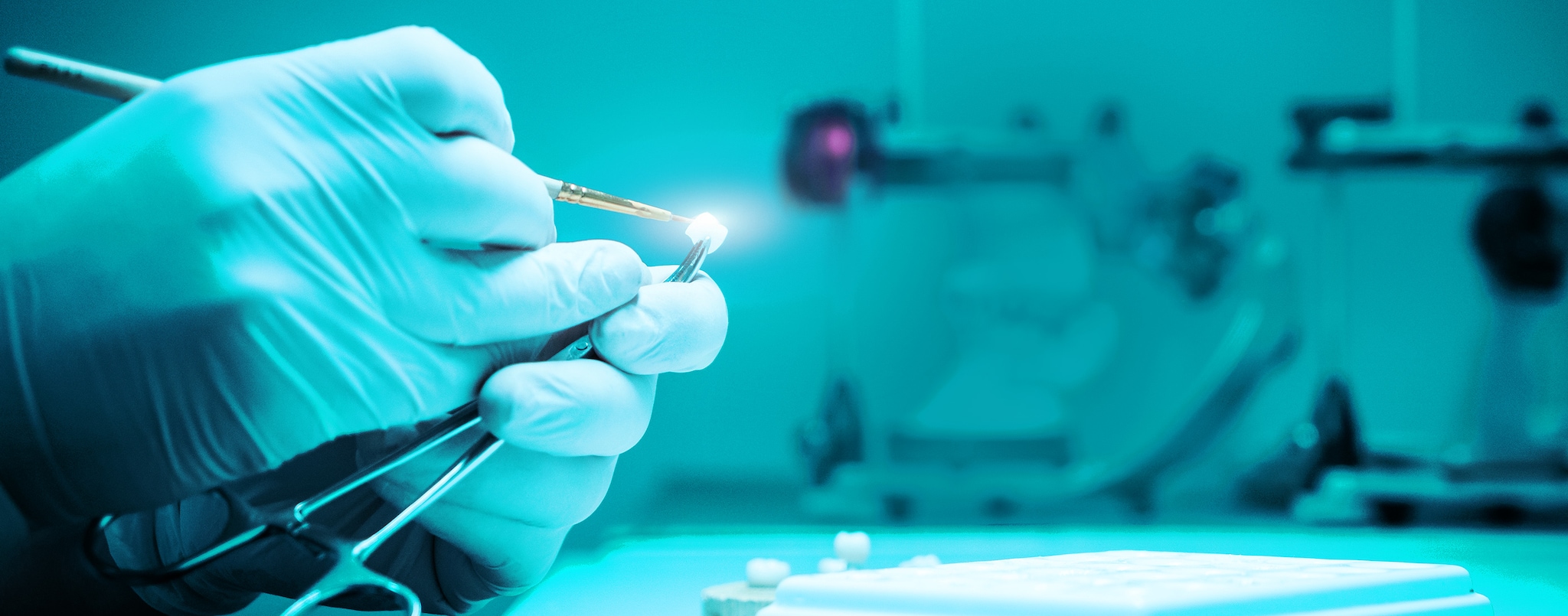
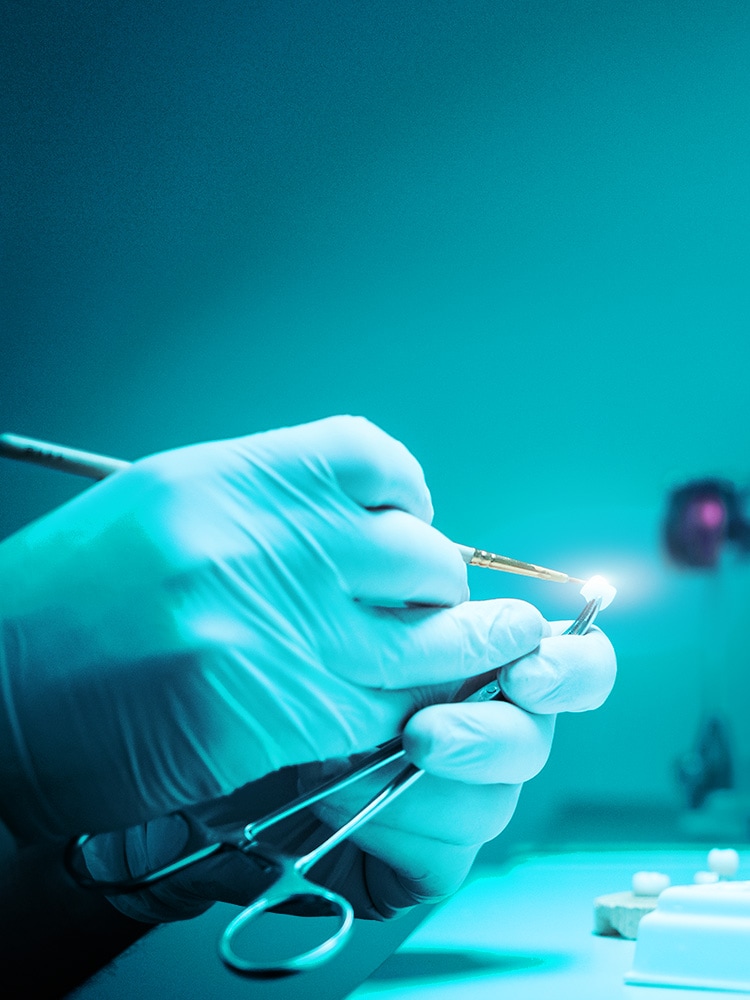
The Potential of Cold Plasma, Expected to be Utilized at the Forefront of Medical Care
Recent years have seen expansion in the use of plasma technology. The development of applications that take advantage of the characteristics of plasma is advancing in many areas, such as semiconductor manufacturing, sterilization and disinfection, and medical frontlines. CeraPlas®, a plasma generator developed by TDK, can generate cold plasma*1 in a compact package and with lower power consumption compared to conventional products. It is expected to catalyze the creation of devices that will make plasma technology more accessible.
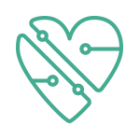
What is plasma? Its features and applications
You may have heard the term plasma before, but most are probably unfamiliar with its details. Plasma is the fourth state of matter, which is neither solid, liquid, nor gas. It refers to a condition in which electrons are separated from atoms and ions, where the electrons become intermixed when high energy is applied to a gas. Familiar examples of plasma include lightning, auroras, and candle flames, and it is said to comprise more than 99.9% of the matter that makes up the universe.
In our everyday lives, it is used in lighting such as fluorescent lamps and neon tubes, as well as in metalworking like arc welding in factories.

The growing possibilities of cold atmospheric pressure plasma
Advances in plasma technology have enabled the stable generation of plasma at low temperatures and atmospheric pressures, which used to be possible only in specialized environments such as a vacuum or in high temperatures. To differentiate from conventional high-temperature plasmas, these are referred to as cold atmospheric pressure plasmas (cold plasmas).
Cold plasmas can have a variety of effects when irradiated on materials. They can clean and sterilize objects by decomposing organic materials, help inks and coatings adhere uniformly to materials by increasing their wettability, or increase the strength of adhesives by activating surfaces.
Because of these characteristics, cold plasmas are used in semiconductor manufacturing and in a variety of other industrial equipment. Additionally, the ability of plasma technology to clean and sterilize surfaces without chemicals makes it very safe, holding the potential to be used in a broader range of fields, including food and medical equipment.
However, conventional cold plasma generators have required high voltages, necessitating separate transformer components and high-frequency generators, resulting in large equipment sizes and high power consumption.
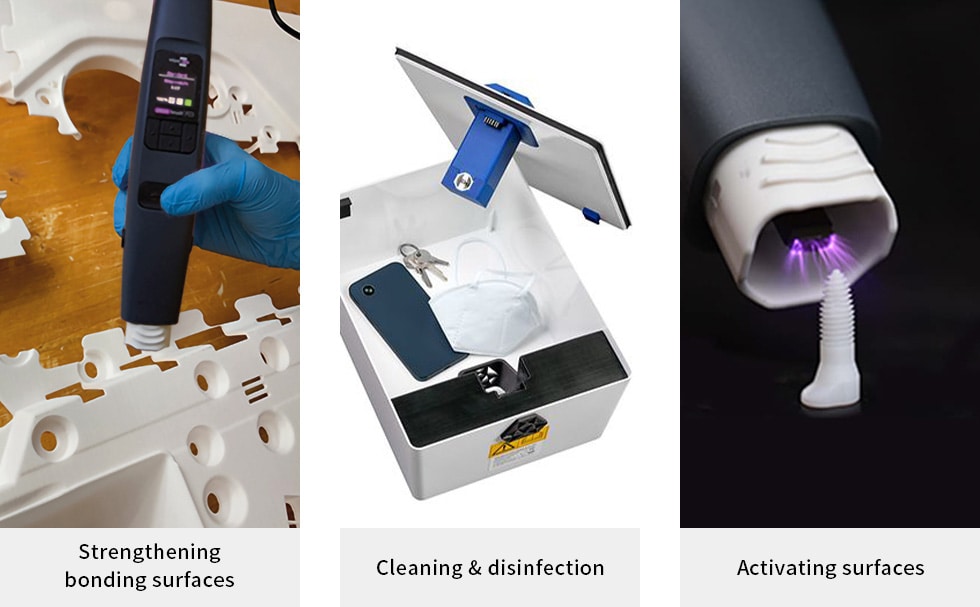
Developing a groundbreaking, compact plasma generator
TDK has developed CeraPlas, the world’s first plasma generator using a piezoelectric transformer*2, by leveraging its long-accumulated know-how in mass production techniques for piezoelectric actuators*3 and multilayer ceramic technologies*4. This groundbreaking product was brought to life through joint development with relyon plasma in Germany, a TDK group company and a leading manufacturer of plasma generators.
With CeraPlas, the voltage step-up function using a piezoelectric transformer and a plasma generator have been successfully integrated through a unique manufacturing method, resulting in a compact, lightweight, low-power plasma generator.
CeraPlas is housed in a compact, stick-shaped enclosure measuring 70.6 × 6 × 2.75mm, and operates on a 12-volt power supply, eliminating the need for special power supplies. This will contribute to the miniaturization of plasma generators based on CeraPlas.
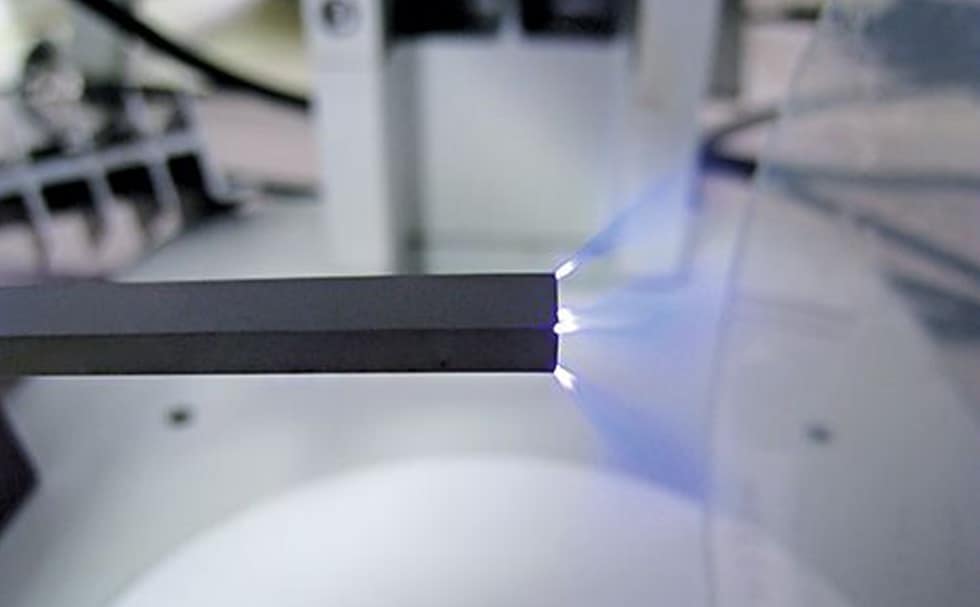
piezobrush®, developed by relyon plasma, is the first plasma generator based on CeraPlas. piezobrush is compact, lightweight, and can be held in one hand like a pen for easy operation. Dr. Stefan Nettersheim, General Manager of relyon plasma, spoke about the strengths of piezobrush. “A small, portable plasma generator like piezobrush was made possible by TDK’s CeraPlas. We were able to design the power supply and drive circuitry as a very compact module, without requiring large drive circuitry or cooling systems.”
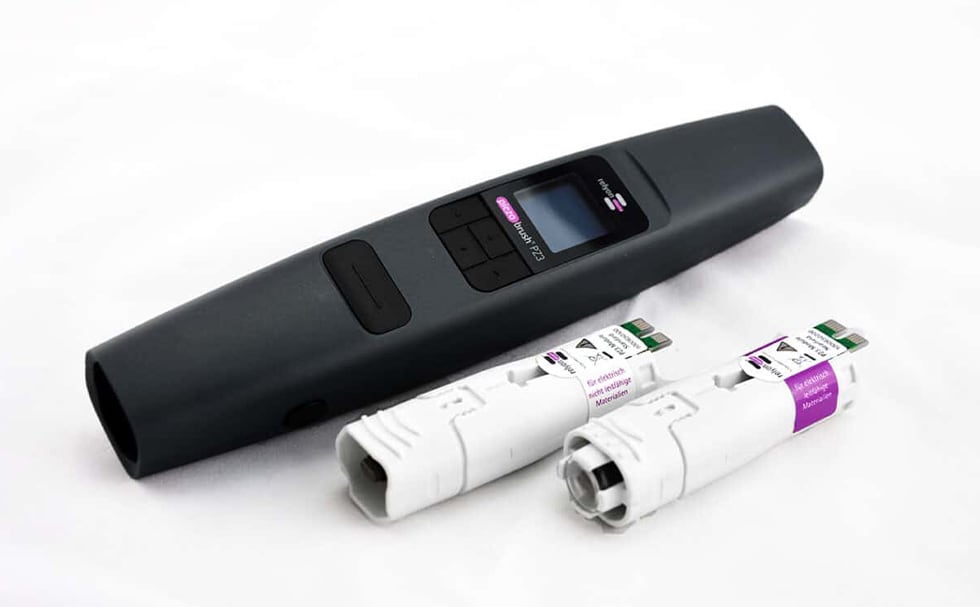
Toward medical applications and use in a wide variety of other fields
piezobrush, with its hand-held operation and ability to work on minute details, will enable the use of plasma in areas where it was previously challenging to do so. One such area is the treatment of dental implants. When cold plasma is used to bond disparate materials or to color dentures, the bond strengths can be increased and the uniformity of coloring can be improved by increasing the wettability. Furthermore, studies have shown that the increased wettability of implant surfaces can improve affinity with biological tissues. This has garnered particular attention in Europe, where dental technology is highly advanced.
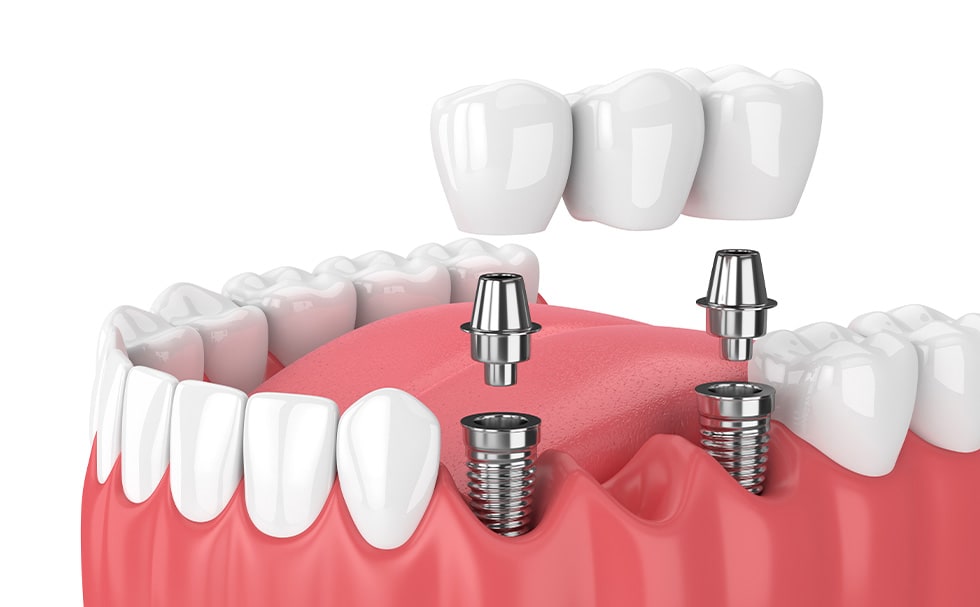
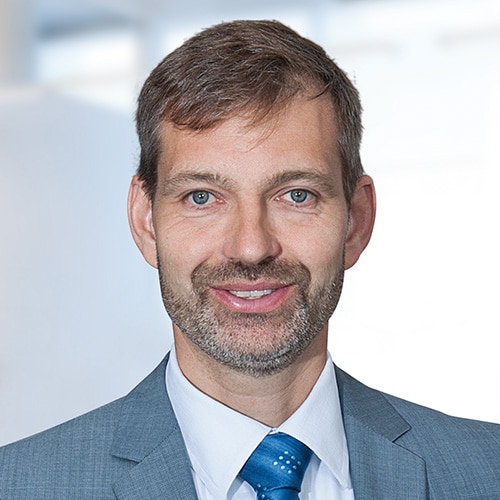
General Manager
relyon plasma GmbH
Cold plasma is applicable to a vast range of fields, including manufacturing, surface activation of plastics and treatment of dental implants. Dr. Nettersheim continues, “piezobrush, based on CeraPlas which is compact and features low power consumption, has made plasma more accessible. In the future, we can expect a wide range of applications, including in the medical field. The possibilities of cold plasma will continue to expand.”
CeraPlas® & Piezobrush® PZ3
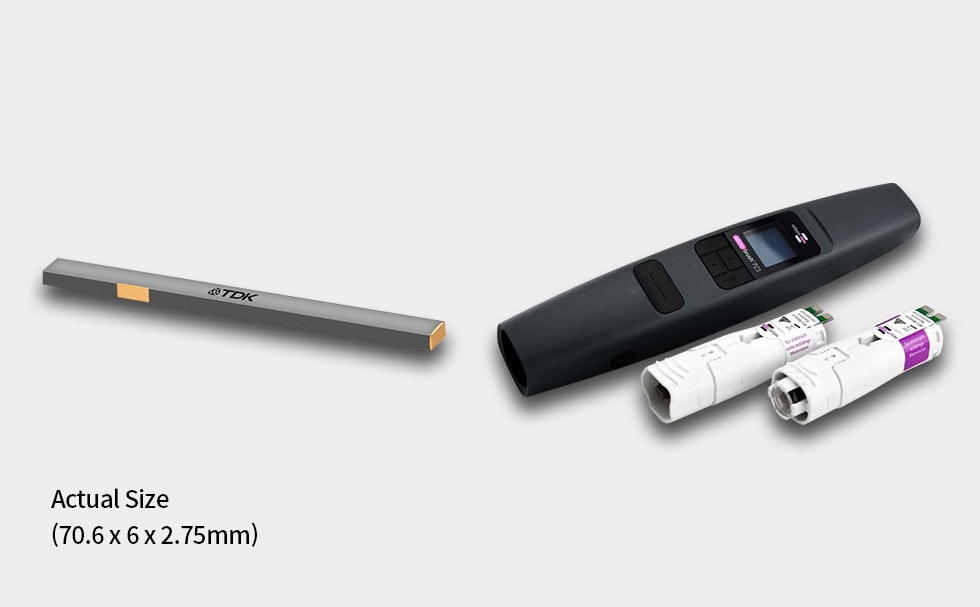
Terminology
- Cold plasma: A plasma in which only the electron temperature is high is called a non-thermal equilibrium plasma (cold plasma). This is in contrast to a thermal equilibrium plasma (thermal plasma), in which the electron temperature and the temperatures of the gas and ions are in equilibrium. The high electron temperature is effective for sterilization, cleaning, and surface activation.
- Piezoelectric transformer: A device that utilizes the properties of piezoelectric ceramics to convert voltages.
- Piezoelectric actuator: A component used to extract mechanical energy by applying a voltage to a piezoelectric ceramic material, a reversal of the phenomenon where the material generates electricity when force is applied.
- Multilayer ceramic technology: A technology essential to the manufacture of multilayer ceramic chip capacitors (MLCCs). Refers to a series of production technologies in which ceramic raw materials are formed into sheets, internal electrodes are printed, layers of them are stacked in large numbers, pressed, cut and fired.
