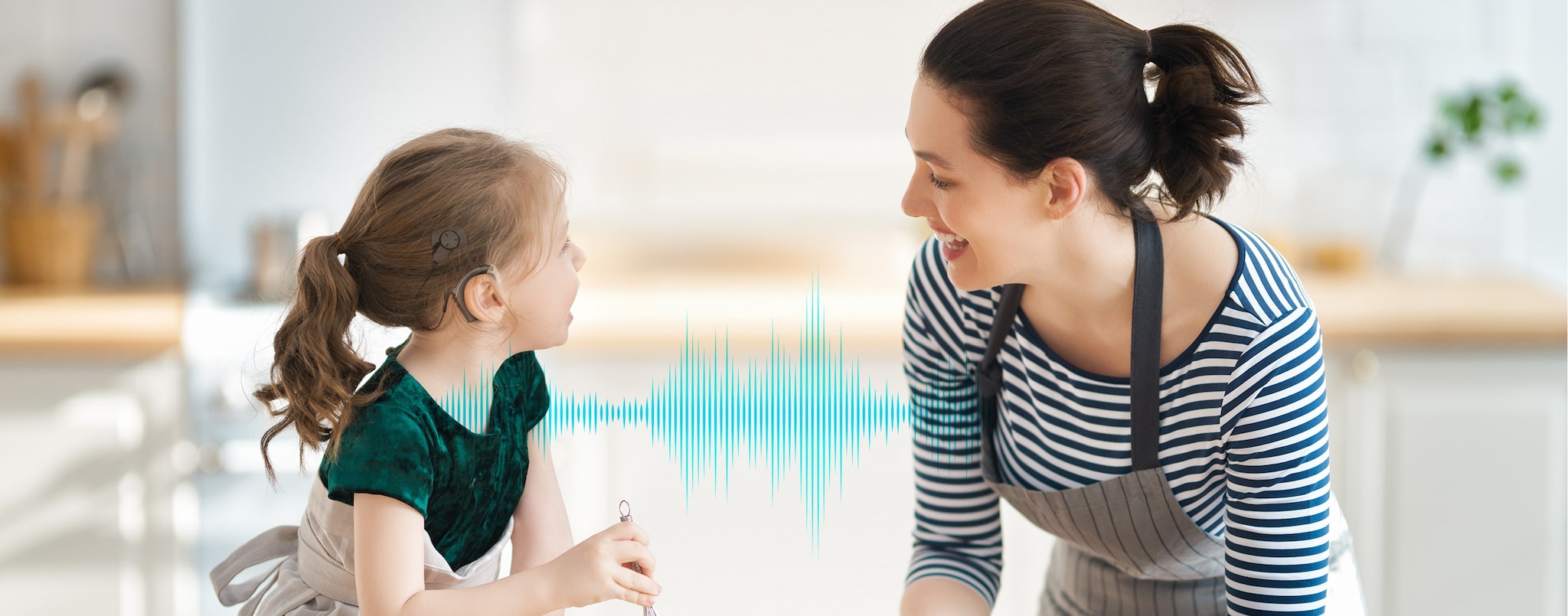
Developing ICs for a Leading-Edge Medical Technology: Cochlear Implants
Artificial organs support the lives of people with physical disabilities, and help improve their qualities of life (QOL). Cochlear implants — said to be the most advanced of all artificial organs — are electronic devices that are embedded and operate inside the body, and require highly accurate and reliable integrated circuits (ICs) *1. The following is a behind-the-scenes look at the development process at ICsense, a supplier specializing in application-specific integrated circuits (ASICs) *2 for use in medical equipment as well as a variety of other electronic devices for the consumer, automotive and industrial markets.
(Footage: Newsflare)
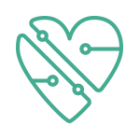
The Cochlear Implant and How It Supports the Lives of the Hearing-Impaired
Cochlear implants are designed to mimic the function of a healthy inner ear (or cochlea). Their performance has improved dramatically, enabled by electronic components that keep shrinking in size and growing in sophistication. They replace the function of damaged sensory hair cells inside the inner ear to help provide clearer sound than what hearing aids can provide.
A cochlear implant system has two parts. One is the external sound processor, which includes two microphones that capture sound and converts it to electrical signals that are sent to an internal implant. The other is the implant that is surgically placed under the skin and attached to an electrode array that is placed in the cochlea, which receives the electrical signals transmitted by the external sound processor and sends them on to the hearing nerve in the brain. For many of those with hearing loss, it is an indispensable device for going about their daily lives.
How a cochlear implant works

Image courtesy of Cochlear Limited
1. Microphones on the sound processor pick up sounds and the processor converts them into digital information
2. This information is transferred through the coil to the implant under the skin
3. The implant sends electrical signals down to the electrode in the cochlea
4. The hearing nerve fibers in the cochlea pick up the signals and send them to the brain, giving the sensation of sound
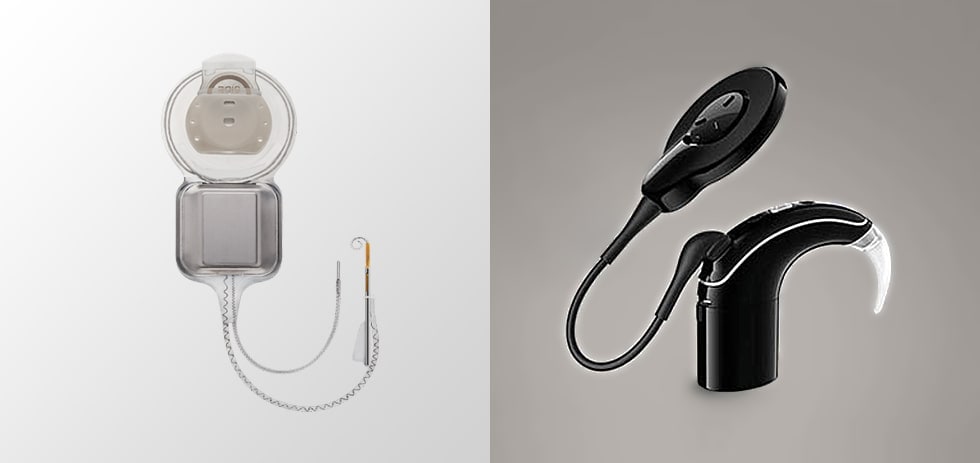
Images courtesy of Cochlear Limited
Why Cochlear, a Leading Company in Cochlear Implants, Chose ICsense
Cochlear Limited, headquartered in Australia, introduced the world’s first commercial cochlear implant, and has continued to improve its performance over many years. Since its founding in 1981,Cochlear has provided more than 600,000 implantable devices, helping people of all ages, in more than 180 countries, to hear. Over a decade ago, Cochlear made the decision to work with ICsense, a TDK Group company specializing in custom ASIC development, as a key component supplier to design and develop ASICs for its cochlear implant products.
“We chose ICsense not only for their technical competence, but for their experience designing for implantable medical uses, and especially because we were able to collaborate in an open manner,” according to Carl Van Himbeeck, a General Manager at Cochlear. “This enabled us to work iteratively together towards optimal designs for our goals.”
Cochlear’s implants incorporate ASICs designed by ICsense that include power management, circuitry that generates programmable analog signals delivered to the electrodes connected to the auditory nerve, and circuits for detecting the body’s minute neural responses—called Neural Response Telemetry (NRT)—that are measured in microvolts.
Jeroen Van Ham, Senior Business Development Manager at ICsense, emphasizes the distinct advantage they have with mixed-signal *3 designs that bridge the analog and digitals worlds. “Low-noise, low-power, and small size are all paramount to high-performance, battery-powered devices. Developing circuits that link the analog and digital domains has been the focus of our expertise over the last 15 years. There are not many companies in the world with our size and capability that are able to design analog, digital, and high-voltage circuits.”
Designing and Developing ASICs Customized for Customer Needs
ICsense is certified under ISO 13485 *4, an international standard for quality management systems for the development of medical devices. Van Ham explains the cooperation model with Cochlear. “To make state-of-the-art medical development a success, you need to work very closely with the customer. Given the additional design and verification, safety reviews, and reporting required for high-reliability medical devices, the overall development process takes longer. Our collaboration with Cochlear is far more than a typical vendor-customer relationship.”
ICsense refers to its process of maximizing product value by aligning to customer needs as “tailored” development. Just as it does for customers in the medical field like Cochlear, ICsense continues to develop custom ICs for each customer—whether they be in automotive, industrial, or consumer markets—like bespoke suits.
The ASIC development process
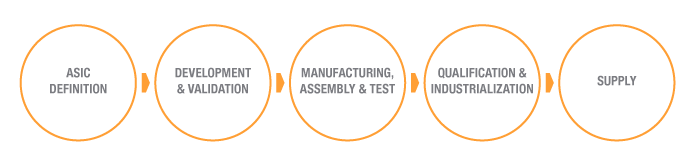
Van Ham is enthusiastic about the future as well. “Over 50 years ago, we embarked on the journey of enabling hearing-impaired people to hear. In the future, I believe we will be able to help those who have lost their vision to see again. It’s a different challenge, but I see it already beginning.”
ICsense will continue to develop highly sophisticated IC solutions to meet the many challenges in this world. One minuscule chip holds the potential to change our future in a gigantic way.
For more examples of ASIC development and details on their technologies, please visit the ICsense web site.
Terminology
- IC: Short for Integrated Circuit, a set of electronic circuits composed of elements such as transistors, diodes, resistors, and capacitors, formed on a single chip.
- ASIC: Short for Application Specific Integrated Circuit, an IC that combines functionalities for a specific use.
- Mixed-Signal IC: A semiconductor circuit that processes both analog and digital signals on a single chip.
- ISO 13485: An internationally-recognized standard for quality management systems for medical devices. Requirements for documentation, quality management practices, and risk management are far more thorough compared to ISO 9001. It is a foundation for ensuring the quality, reliability and safety of medical devices.
