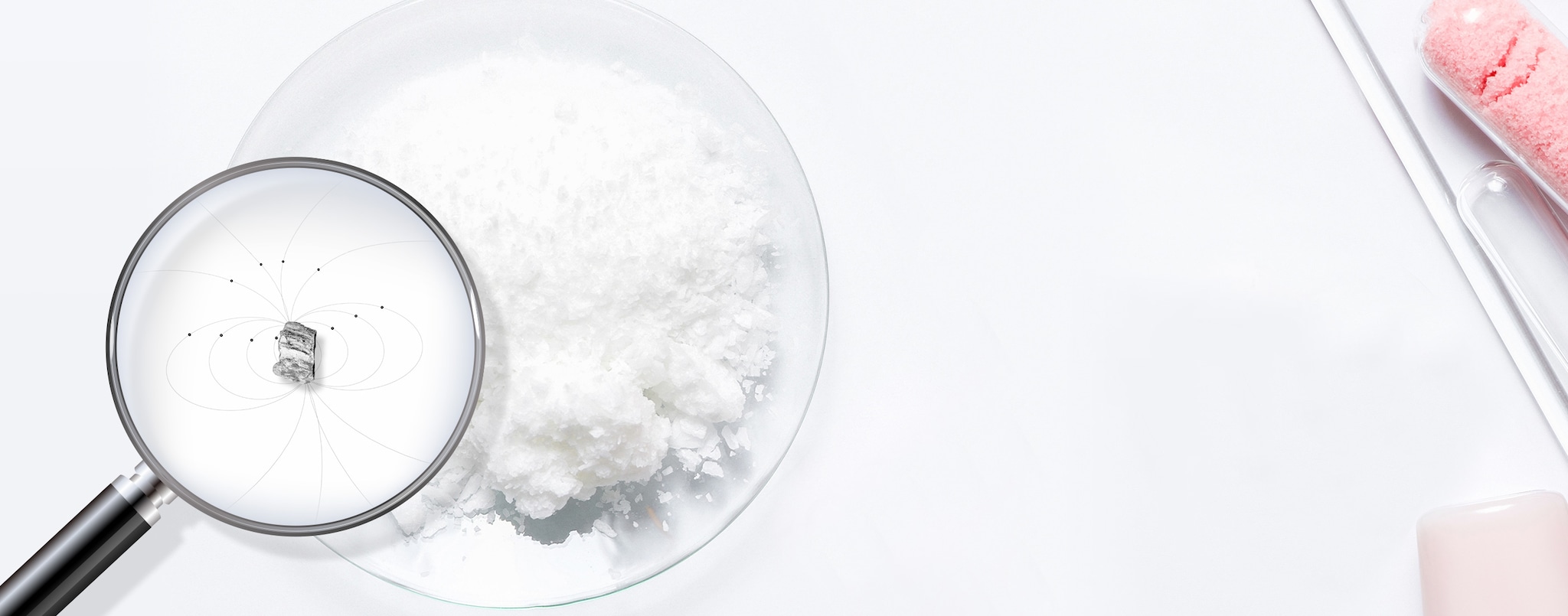
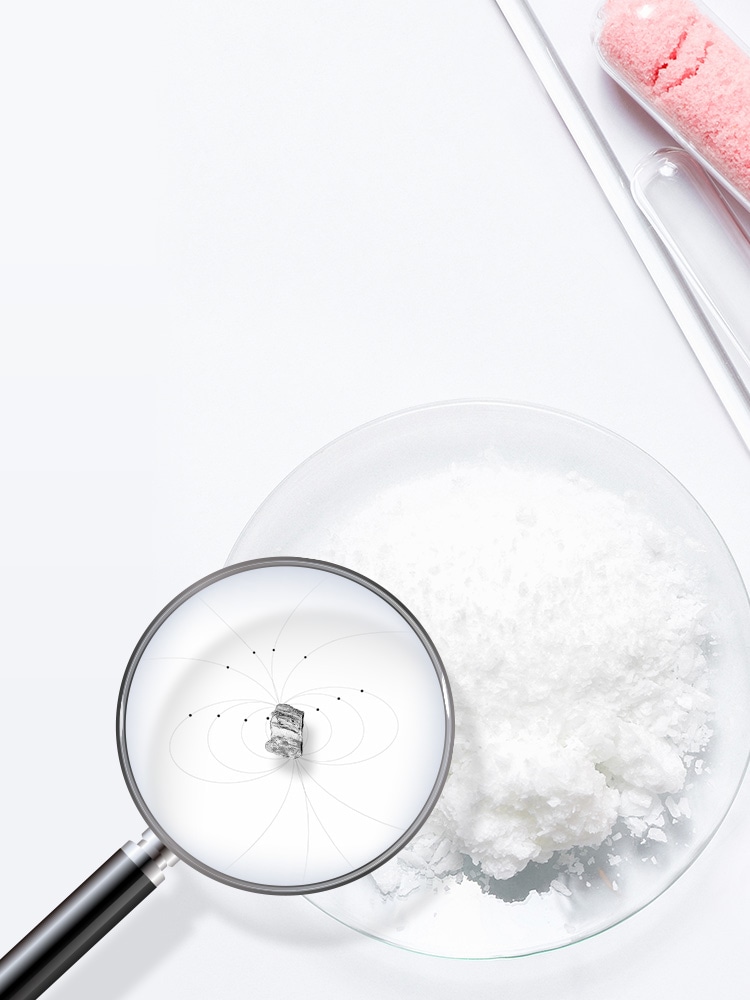
Compact, High-Performance Magnetic Sensor Will Not Miss Even a Speck of Metal Smaller Than 0.1 mm
At the forefronts of manufacturing, preventing contamination by microscopic foreign object debris through the implementation of thorough quality control from the raw materials stage is critical to ensuring the stable production of quality products. For a variety of products, factories have been utilizing a plethora of inspection methods and sensors to remove minuscule debris invisible to the human eye. TDK has newly developed a highly sensitive, compact magnetic sensor capable of detecting metal fragments smaller than 0.1 mm by applying the technologies it has amassed in the manufacturing of hard disk drive heads.
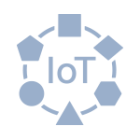
Related Stories:
The magnetic sensor detects one ten-millionth of geomagnetism
[Sustainability and TDK] Ultra-Sensitive Magnetic Sensor Component Has Potential to Unlock New Possibilities for Medical 3D Imaging
How important is debris inspection in manufacturing?
To improve product quality, manufacturers of pharmaceuticals, cosmetics and industrial chemicals pay close attention to the adhesion and intrusion of foreign object debris both large enough and too small to be visible to the human eye.
Even the tiniest speck of debris can trigger serious consequences in our everyday lives—for example, a microscopic contaminant in the ingredients of a smartphone’s lithium-ion battery can cause capacity degradation, heat generation, or even ignition.
A wide range of methods exists for detecting microscopic debris. Inspection using cameras and image sensors is growing more sophisticated with advances in image processing and the integration of AI. Optical inspection, however, is limited to the detection of debris present on surfaces. Ultrasonic inspection can examine the interior of objects, but resolutions are usually defined in millimeters—inadequate for detecting smaller particles.
X-ray equipment is widely used today to detect microscopic foreign object debris. By irradiating X-rays onto the inspection target, both surface and internal debris can be detected quickly. While metals as well as non-metals like glass, rubber and plastics are detectable, their sizes are limited to several hundred µm (tenths of a mm) at best—which explains why there is a growing need for sensors capable of finding debris smaller than 100 µm (0.1 mm) in order to support more sophisticated, higher-quality products.
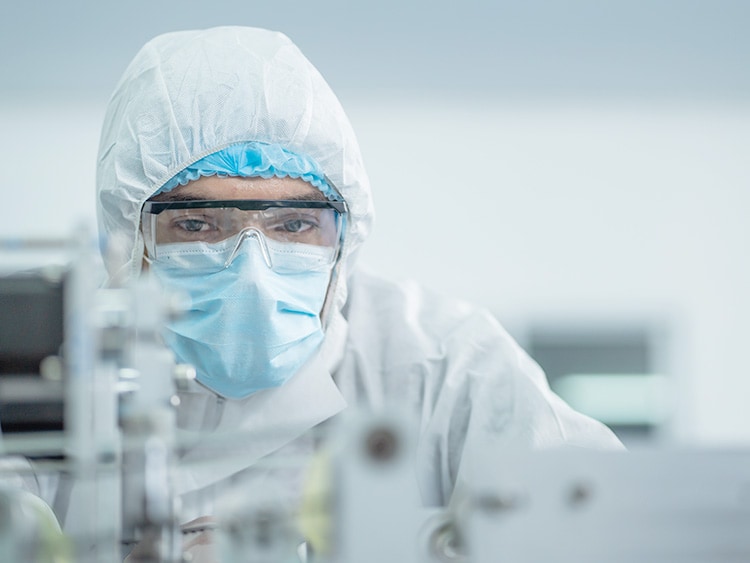
Types of inspection for foreign object debris and their working principles
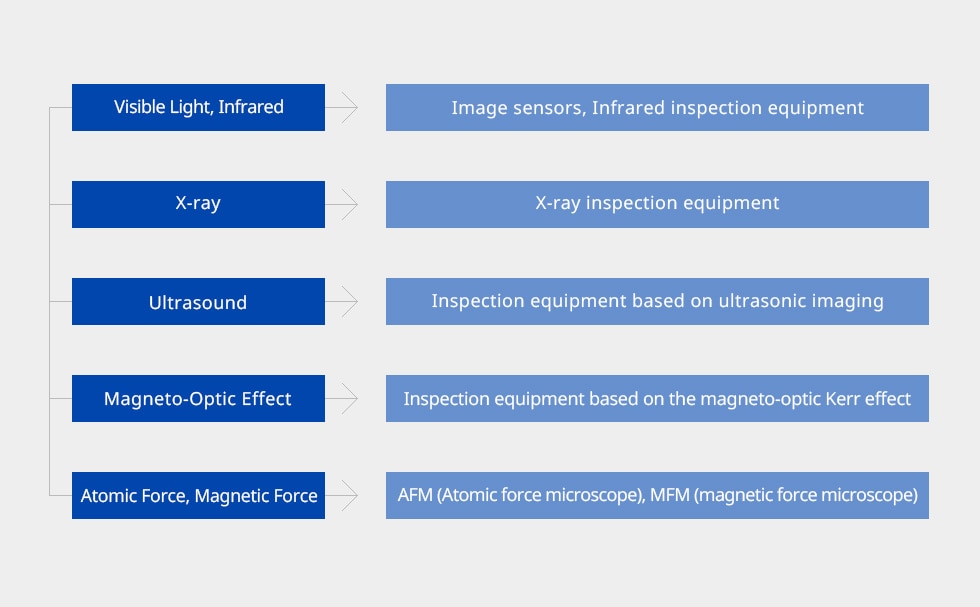
The need to detect iron and stainless steel
In today’s manufacturing environment, there is a growing demand for the ability to detect iron and stainless steel particles smaller than 200 µm (0.2 mm). Because non-magnetic metals like aluminum and copper are viscous and tend not to become fine particles, external contamination can be prevented by raising the cleanliness of factories. Iron and stainless steel, however, are difficult to eliminate as they are used as materials in production equipment, and operating them inevitably generates fine particles.
To address this problem and meet today’s needs to detect metallic contaminants, TDK has developed the Migne xMR sensor, an xMR*-type magnetic sensor based on the Nivio magnetic sensor. With an improved signal-to-noise ratio in micromagnetic fields compared to Nivio, its size is a mere 8 by 8 by 5 mm—small and thin enough to sit on a fingertip.
Migne xMR sensor—the Nivio magnetic sensor made even more compact
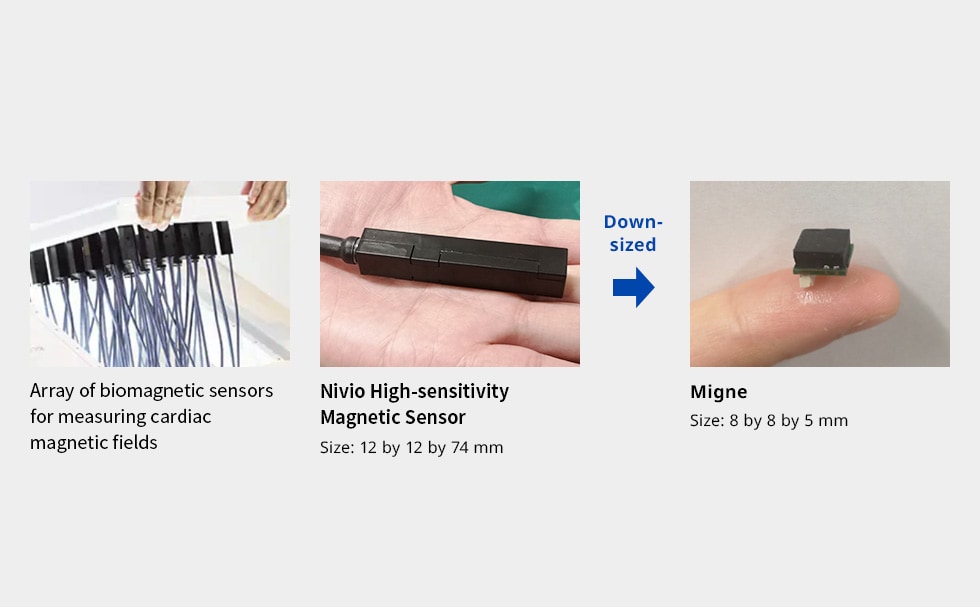
A high-sensitivity magnetic sensor from TDK that reveals the magnetism of magnetic particles conspicuously
A typical system for detecting metallic foreign object debris in a factory production line is as follows. Fine metal powders of iron and stainless steel are generated from the wear and peeling in manufacturing equipment, contaminating the object to be inspected. The system uses a powerful magnet to magnetize the entire object. Metal sensors then detect the magnetism emitted by the metallic debris.
The magnetized metallic particles become tiny magnets with N and S poles. When scanned by the Migne xMR sensor, the outward and inward magnetic field lines are displayed in red and blue, making the magnetized metallic debris detectable.
How a metallic foreign object debris detection system works
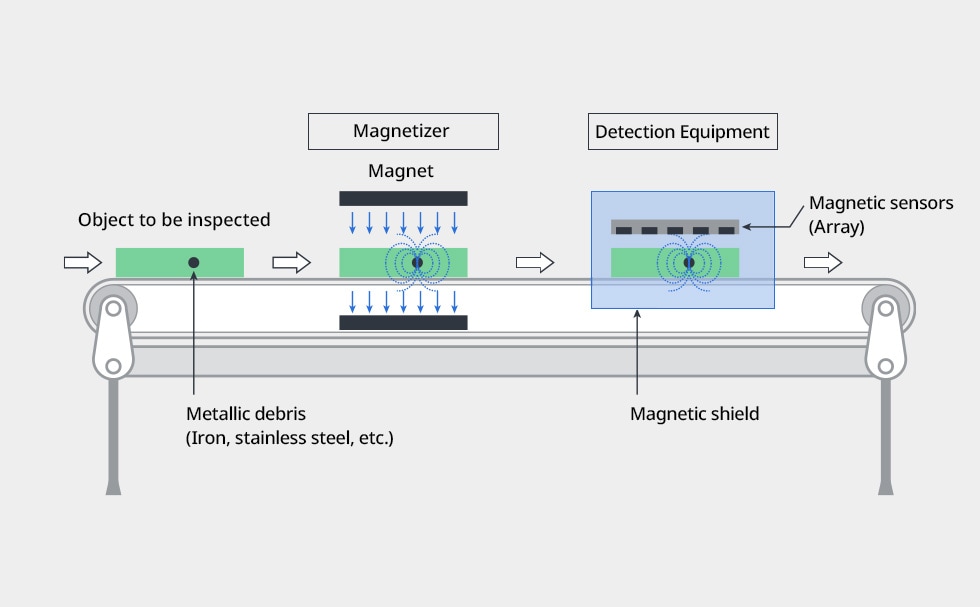
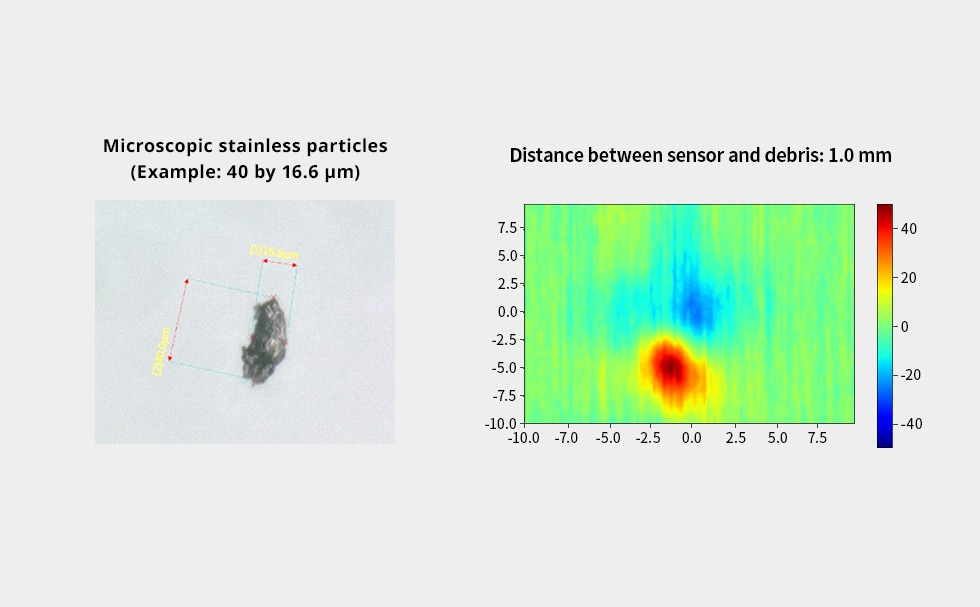
Applications beyond manufacturing
Migne xMR can be used to detect foreign object debris over a wider area by arranging the compact sensor in an array. It can resolve the headaches often encountered with X-ray inspection systems—mainstream in pharmaceutical and chemical manufacturers today, where sophisticated inspection for foreign object debris is required—to improve product quality and safety and reduce defects.
Migne xMR performs exceptionally well in other applications requiring the detection of micromagnetic fields, not just debris inspection. These include prospective uses in nondestructive testing, which refers to the examination of the internal state of an object without destroying it, and in magnetic particle imaging, a diagnostic imaging technology in the medical field. Possibilities abound from TDK’s compact, high-precision xMR sensors.
Terminology
