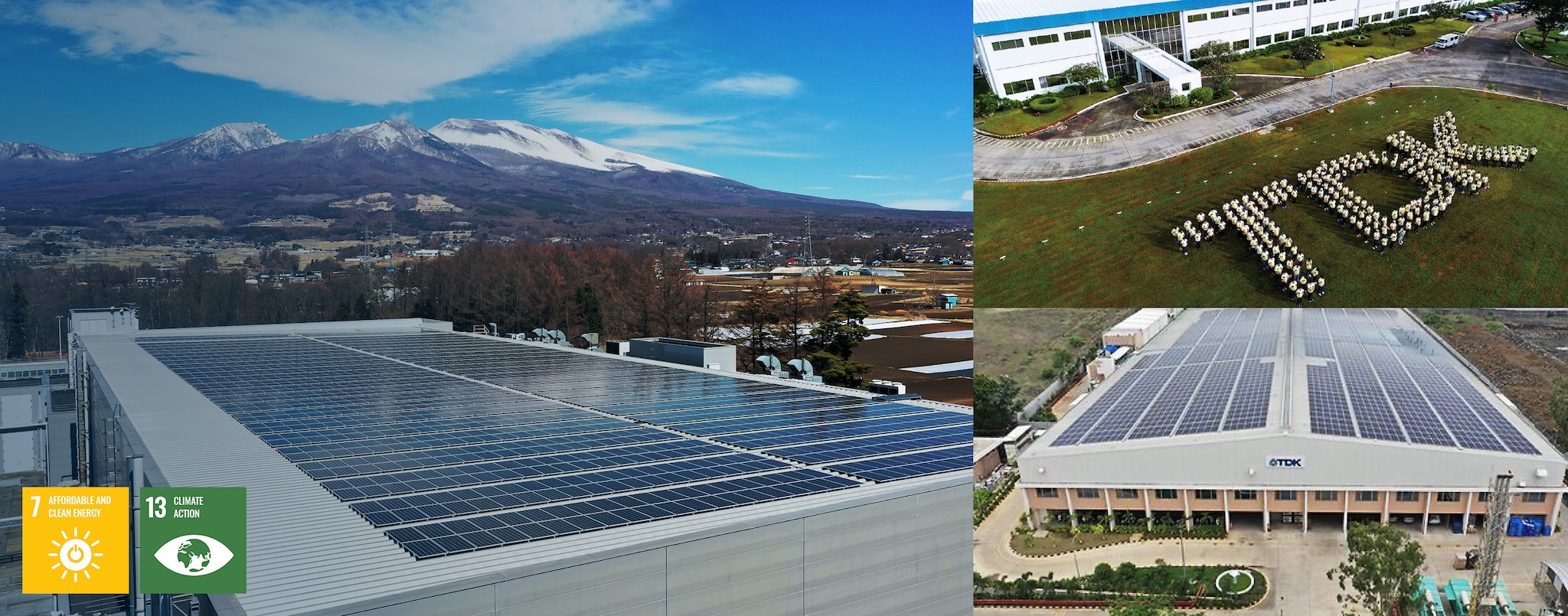
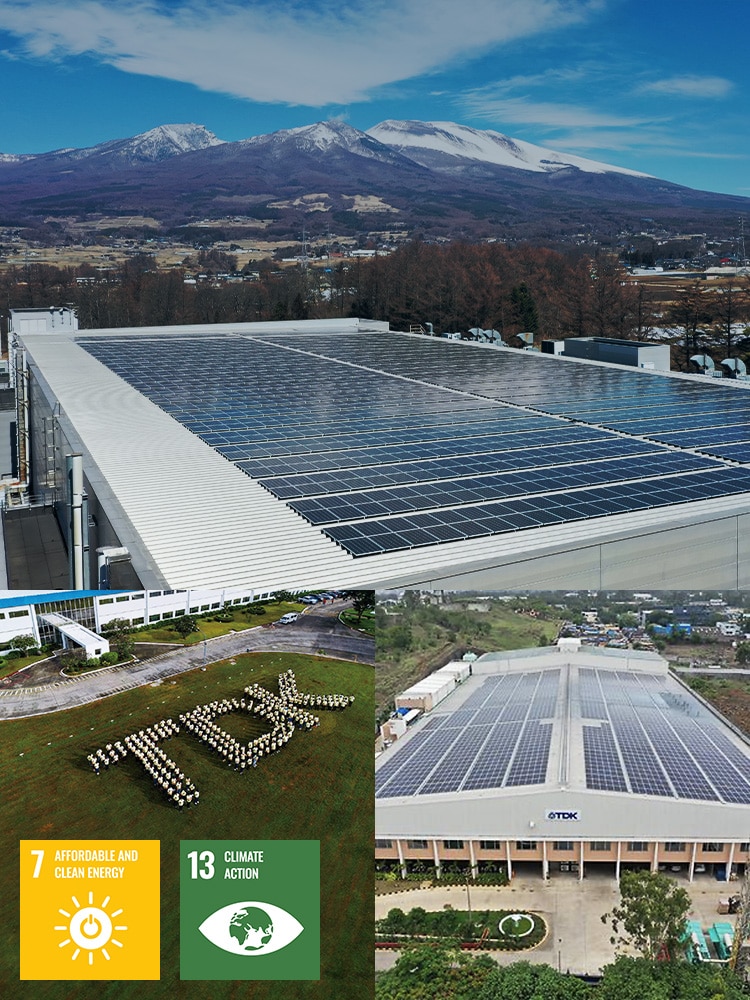
【Sustainability and TDK】
Why Is TDK Serious About Taking On Climate Change? (Part II)
TDK, which manufactures a vast range of products at sites located across more than 20 countries worldwide, is committed to an ambitious goal of raising the ratio of renewable energy to 50% of the group’s total electricity consumption by fiscal 2025 and to 100% by 2050. In July 2023, all 25 manufacturing sites in Japan switched to exclusively using power derived from renewable energy sources. This achievement is particularly noteworthy for a manufacturing enterprise with facilities operating around the clock. The first installment of this series presented an overview of TDK’s strategies to combat climate change. This follow-up piece showcases specific initiatives at TDK’s various manufacturing sites to transition to renewable energy and explores what the future holds.
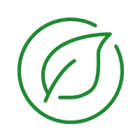
In its medium-term corporate strategy, Value Creation 2023, TDK is working to create value—including Social Value—and seeks to enhance its corporate value by contributing, through its businesses, to resolving global issues set forth in the SDGs.
▶Efforts to Achieve the SDGs
▶Related Stories:
・Why Is TDK Serious About Taking On Climate Change? (Part I)
・What is Being Done at Manufacturing Sites to Reduce CO₂ Emissions?
Importance of adopting renewable energy at manufacturing sites
Amid the growing global interest in decarbonization as a measure against climate change, TDK is striving to achieve sustainable manufacturing to live up to its social responsibility as a manufacturer. The transition to renewable energy is becoming essential among the concrete actions companies can take to reduce CO₂ emissions and alleviate their environmental footprint. TDK is promoting the adoption of renewable energy in ways that are optimal for each manufacturing site, taking into account the local energy circumstances of various regions worldwide.
What is renewable energy?

Asama Techno Factory, Japan (TDK)
Energy conservation and adoption of renewable energy across the entire site
TDK’s Asama Techno Factory (Saku City, Nagano Prefecture) serves as a core plant for TDK’s global magnetic sensor business, developing and manufacturing high-precision, low-power magnetic sensors designed for automotive applications.
To achieve lower electrical power consumption, the factory has launched a project to reduce its energy use. This includes coordinating with production plans to operate equipment more efficiently, implementing waste heat recovery systems, optimizing air conditioning based on usage, and instituting power leveling. These diverse activities culminated in a 25.3% reduction in energy consumption (as of the end of June 2019, compared to 2015). In recognition of these efforts, the factory was honored with the Chairman’s Award from the 2019 Energy Conservation Awards (organized by The Energy Conservation Center, Japan, and backed by Japan’s Ministry of Economy, Trade and Industry).

In 2022, the factory was recognized by Nagano Prefecture as an “Excellent Contributor to Global Warming Prevention” for the installation of solar panels and other energy conservation efforts. In 2023, TDK completed construction of a new facility equipped with solar panels, reaching the milestone of sourcing 100% of the electricity used at the plant from renewable energy. As an advanced environmentally-conscious facility within TDK, the factory is committed to further energy savings.
Solar panels on the roof of the Asama Techno Factory
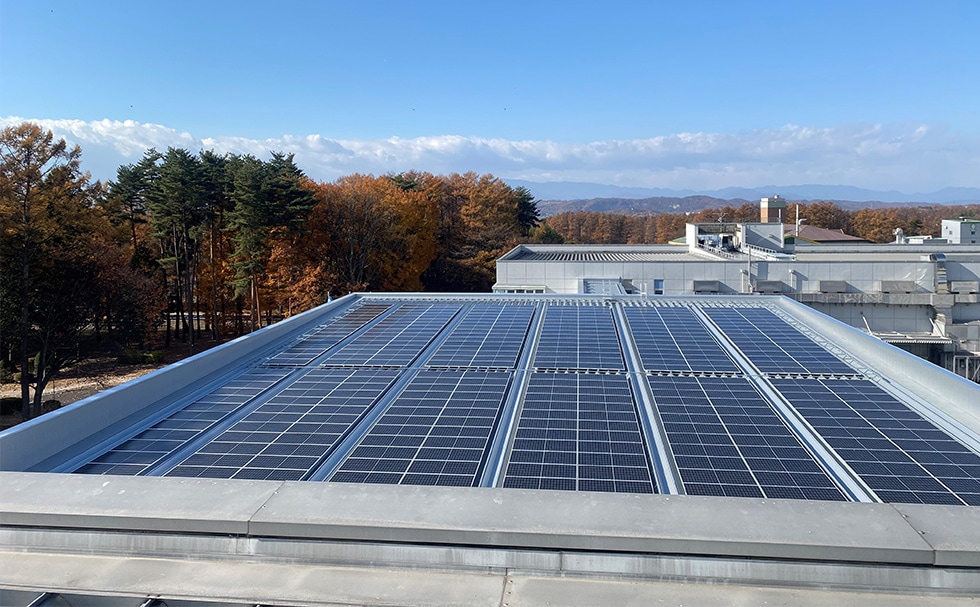
Nashik Factory, India (TDK Electronics)
A state-of-the-art factory practicing both sustainable production and “Monozukuri” craftsmanship
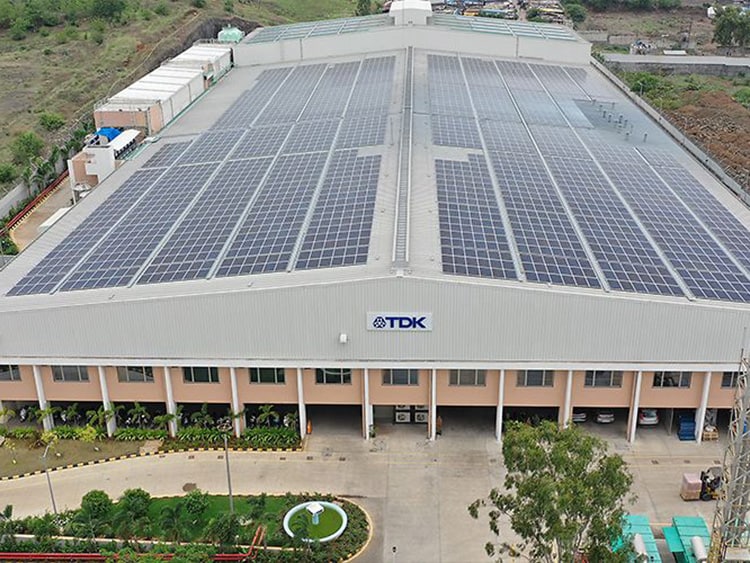
The Nashik Factory (Maharashtra, India) is a major manufacturing base in the rapidly growing Indian economy, characterized by the latest in production equipment and its environmental friendliness. Since commencing operations in 1996, the plant has been manufacturing various film capacitors, including AC/DC capacitors, PFC capacitors and their key components, and capacitors for power electronics.
The factory strongly emphasizes environmentally-conscious manufacturing processes and promotes the adoption of renewable energy as part of that commitment. In addition to the existing solar panels on the production building’s roof, a solar power generation system—the largest of its kind at a TDK site—became operational in 2021. Today, roughly half of the energy used in the factory is sourced from renewable energy. This has resulted in a reduction of approximately 8,200 tons of CO₂ emissions annually.
Using renewable energy from a large-scale solar power generation facility
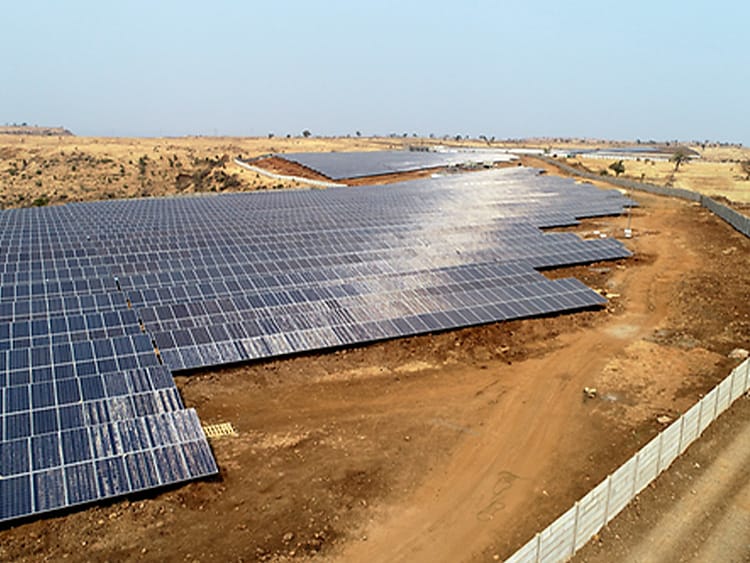
Laguna Factory, The Philippines (TDK Philippines)
A flagship base in Southeast Asia engaged in a wide range of products
TDK Philippines Corporation (TPC) began operations in 1996 as a primary manufacturing base for HDD magnetic heads and has been steadily expanding its operations. Assembly of Camera Module Actuators (CMAs) for smartphones began in 2014, followed by the production of inductors starting in 2016. Subsequently, TPC has diversified its manufacturing portfolio to include prototypes of biomagnetic sensors, mass production of electric double layer capacitors, power inductors, and automotive SMD transformers. It has grown into a core manufacturing base for TDK in Southeast Asia, adding to its production lines Head Gimbal Assemblies (HGAs) for MAMR, a next-generation Hard Disk Drive (HDD) technology.
The Philippines is known for having multiple volcanos and geothermal resources, and geothermal power is drawing interest as a form of renewable energy capable of providing a stable supply of electricity. The country hosts numerous geothermal power plants, boasting the world’s third-largest geothermal power capacity after the United States. (Source: World Geothermal Congress 2020 Update Report)
In 2022, TPC entered into a power purchase agreement with First Gen, a leading renewable energy supplier, successfully transitioning its power consumption to be sourced 100% from geothermal energy. This initiative is expected to reduce CO₂ emissions by 12,000 tons annually.
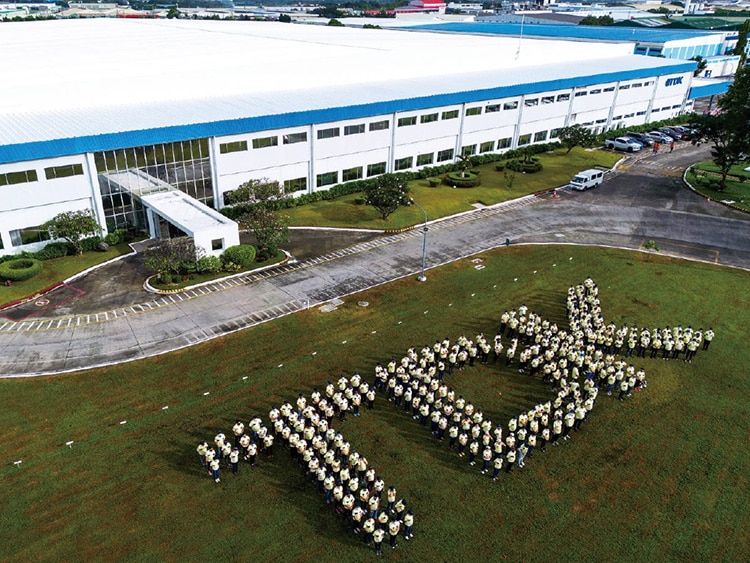
Changes in CO₂ Emissions at TDK Philippines
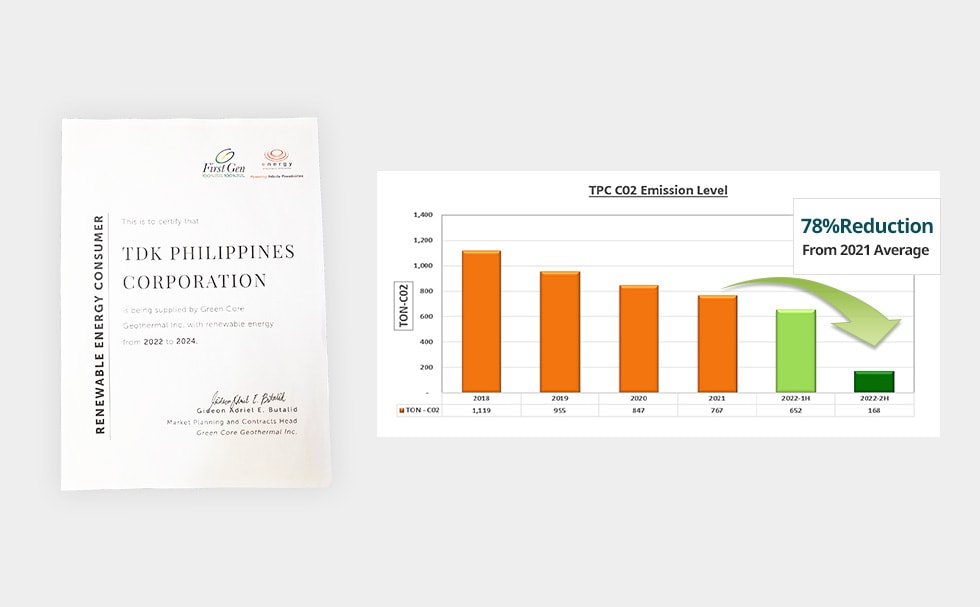
Right: Significant reductions in CO₂ emission are expected by switching to geothermal-derived electricity.
Moving towards electricity derived from renewable energy at all sites
In July 2023, TDK successfully transitioned to electricity derived 100% from renewable energy sources at all of its manufacturing sites in Japan, ahead of other sites around the world. Kenichiro Arimura, General Manager of TDK’s Procurement & Logistics Group, explains how the transition was achieved.
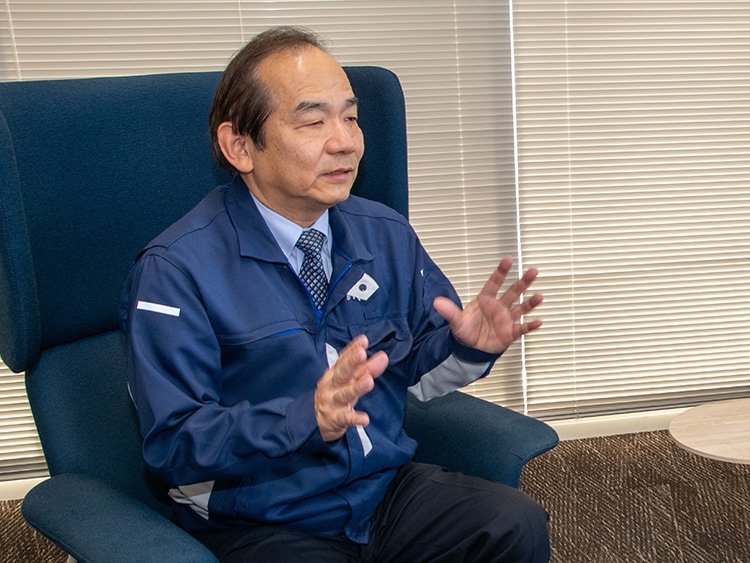
“Until last year [2022], the proportion of renewable energy used at our manufacturing sites in Japan was only around 5%. On the other hand, we were advocating the introduction and increased use of renewable energy at our manufacturing sites worldwide and throughout the entire TDK Group. We were also seeking cooperation from our suppliers in reducing CO₂ emissions in the future. Clearly, TDK’s activities in Japan needed to set a better example.” Arimura continued, “While there is a non-negligible additional cost associated with switching to renewable energy, we secured the buy-in of our Business Groups’ management teams on the value of contributing to society.”
Jason Mizell, General Manager of the Safety and Environment Group at Sustainability Promotion HQ, who oversees the transition to renewable energy at TDK Group’s manufacturing facilities worldwide, shared his insights into TDK’s environmental initiatives.
“As a B-to-B company at the middle of the supply chain, TDK is committed to reducing the environmental impact of our products throughout their entire lifecycle, not only by collaborating with our upstream suppliers but also by contributing to energy conservation and weight reduction downstream, in the product use phase. Customers now evaluate suppliers based not only on costs and delivery times but also from a sustainability perspective. TDK is working to reduce overall CO₂ emissions at its Scope 1 and 2* production sites around the world by promoting the shift to renewable energy (RE) alongside Manufacturing HQ’s low energy (LE) activities.”

TDK is increasing the number of production and development sites worldwide that operate entirely on electricity derived from renewable energy sources, constituting approximately 40% of all electricity consumed by the entire TDK Group as of July 2023. TDK intends to continue transitioning to renewable energy at its manufacturing sites, targeting 100% of the entire Group’s power consumption by 2050. As a manufacturing enterprise, TDK is uniquely positioned to contribute to reducing CO₂ emissions through initiatives at its manufacturing sites. Step by step, TDK is advancing toward a sustainable society.
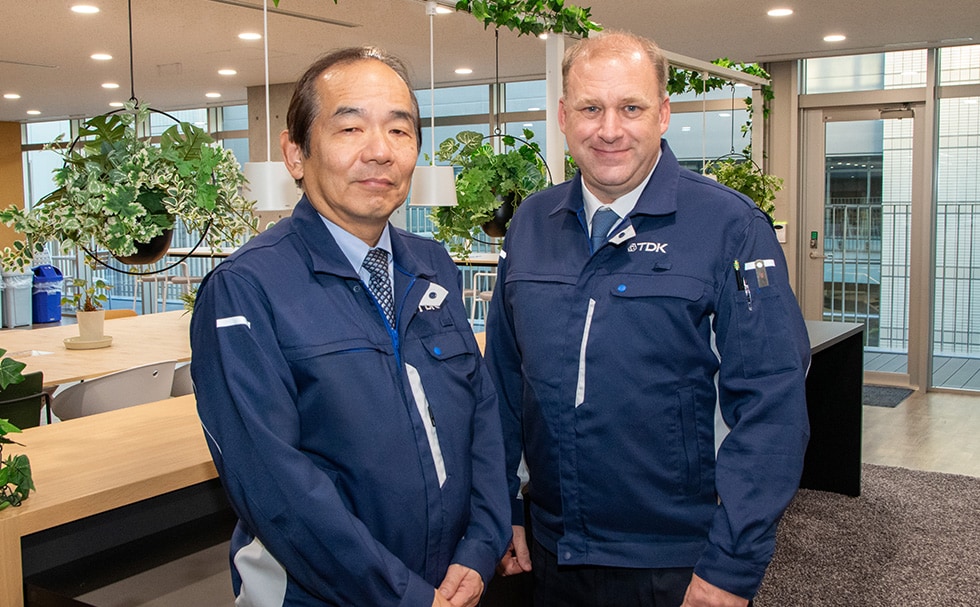
Right: Jason Mizell, General Manager, Safety & Environment Group, Sustainability Promotion HQ, TDK Corporation
Terminology
- * Scopes 1, 2, and 3: Greenhouse gas emissions related to business activities are categorized by scope. Scope 1 refers to direct emissions from industrial processes and their fuel use. Scope 2 refers to indirect emissions from the use of electricity, heat, etc., purchased by the business. Scope 3 refers to indirect emissions outside of Scopes 1 and 2 (emissions by upstream and downstream partners and users).
