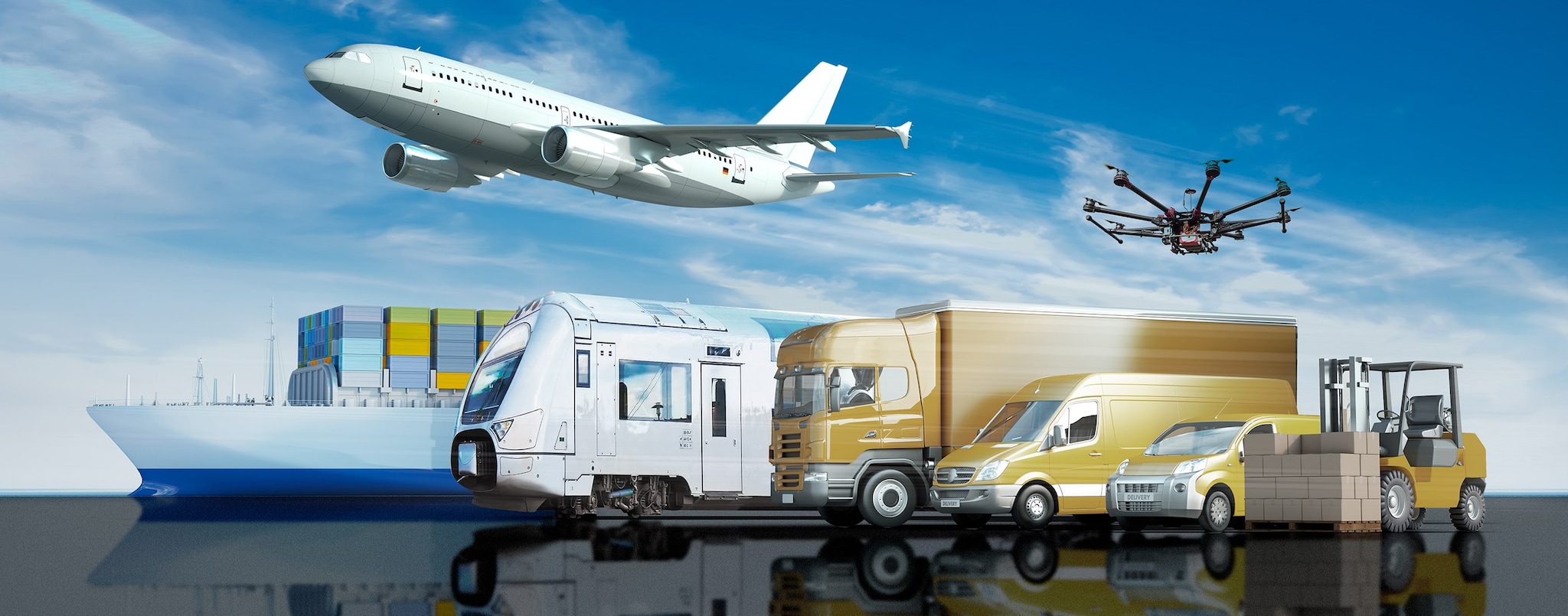
Meet the Fingertip-Sized, High-Precision Digital Sensors that Enable Safe Operation of Drones and Railroads
Inertial sensors are not only used to detect movement in smartphones and game controllers—they also support the safe operation of large transportation systems like airplanes, trains and ships. Because they are used to accurately detect the movement, rotation and tilt of objects, they play an indispensable role in technologies that are sure to greatly change our lives in the future, such as autonomous vehicles and trains, cargo drones, and air taxis. This is why high-precision inertial sensors are under the spotlight.
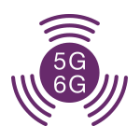
The Rise of Industrial Drones
Drones are expanding into a variety of areas. They are already being used to shoot videos, crop-dust large farms, inspect buildings, and survey sites. In the near future, industrial drones are expected to begin delivering packages and inspecting hard-to-access places, alleviating labor shortages and personnel costs.
Under the banner Industrial Revolution of the Skies, Japan’s Ministry of Economy, Trade and Industry (METI) is eyeing drones as a means to address a variety of social issues, and is working to establish laws and regulations that would allow the widespread use of drones. Similarly, governments around the world are working on deregulation and other measures to support the safe use of drones.
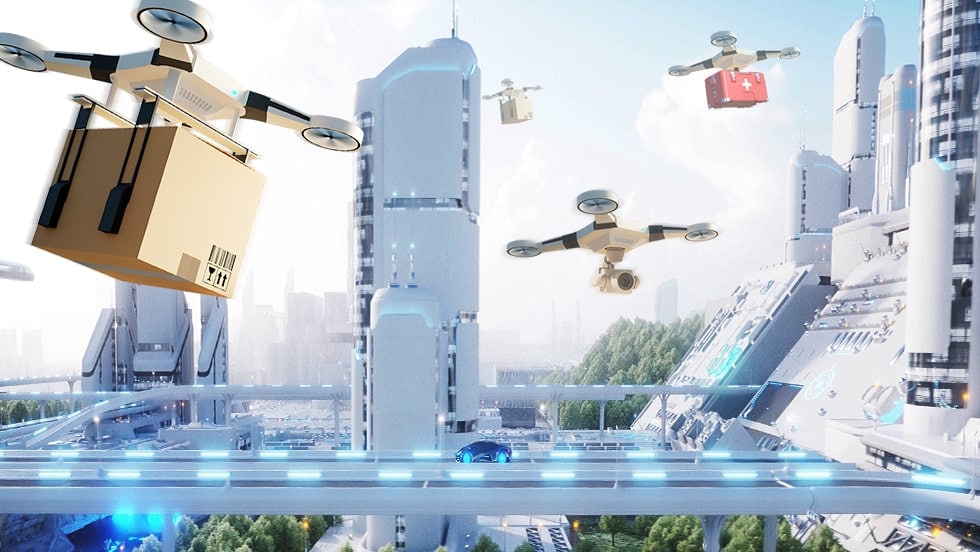
Eyeing the role drones could play in solving social issues, METI has created a roadmap for the widespread use of drones in seven areas: logistics, security, health care, disaster response, infrastructure maintenance and management, surveying, and agriculture, forestry and fisheries.
As industrial drones become more widespread, they are expected to begin flying not only in limited areas, but increasingly over densely-populated urban and residential areas. In order to mitigate the risk of crashes and to ensure safe operation, inertial sensor technologies with ever-higher precision are in need.
Inertial Sensors that Enable Stable Drone Flight
Drones are able to maintain a stable attitude while flying at high speeds, thanks to inertial sensors such as accelerometers and gyroscopic sensors. Accelerometers measure linear acceleration resulting from the movement of objects and from gravity, while gyroscopic sensors detect changes in angle over time. As these sensors constantly detect the aircraft’s attitude and movement, the speeds of the multiple rotors are adjusted accordingly, allowing the aircraft’s attitude to be stabilized and controlled.
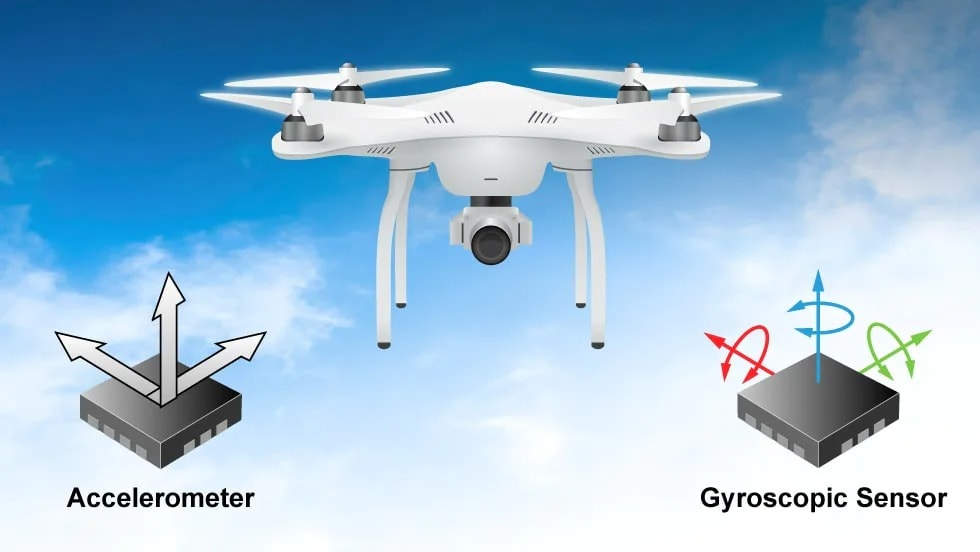
High-Precision Inertial Sensors for Industrial Applications
GNSS (Global Navigation Satellite Systems) such as GPS have been used in car navigation systems to accurately display the car’s position, and are also being used in railroads to precisely locate trains on the track. In situations where satellite signals cannot reach the vehicle, such as tunnels or in between tall buildings, the vehicle’s position can be estimated by augmenting GNSS information with dead reckoning*1 techniques based on information from inertial sensors and odometers mounted on the body.
In environments where there is no reception of GNSS signals, underground excavation machinery and similar equipment can only rely on information from inertial sensors, requiring these sensors to be highly precise. For example, at construction sites and railroads, minimal susceptibility to vibration, shock, dust, and temperature variations are essential to ensure functionality and reliability.
Where high-precision inertial sensors are used
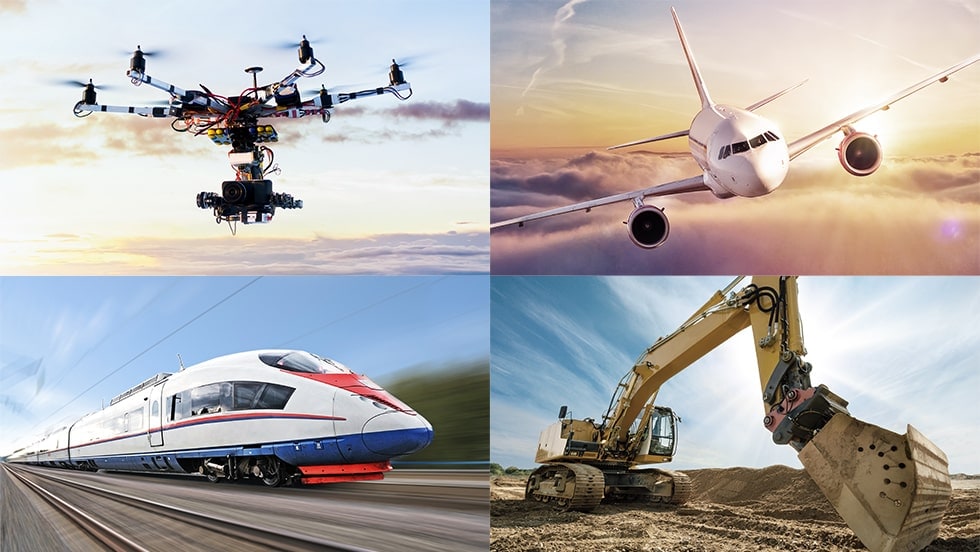
TDK’s Inertial Sensors: High Repeatability in Tough Flight Environments
TDK has been developing and manufacturing high-precision inertial sensors (accelerometers and gyroscopic sensors) for use in autonomous vehicles and train navigation, as well as for avionics*2—specifically, for use in Inertial Measurement Units (IMU) *3 and Inertial Navigation Systems (INS) *4—for flight control of manned and unmanned vehicles. They are among the components essential to flight comfort and safety, requiring high reliability and precision that is unaffected by changes in the environment or over time.
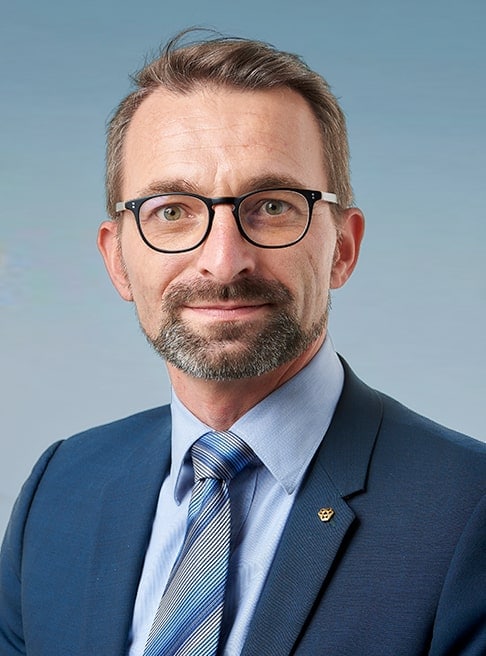
Product Marketing
Tronics Microsystems
Vincent Gaff, in charge of product marketing at Tronics Microsystems, a TDK group company, spoke about TDK’s inertial sensors. “Tronics brand inertial sensors are more precise, more repeatable, and 10 to 100 times less influenced by vibration than typical automotive and consumer inertial sensors. They offer a digital and lower-cost alternative to incumbent analog quartz accelerometers. This makes them well-suited to applications in trains, aircraft, ship navigation, construction equipment and other applications where high precision and long-term stability in tough environments are required.”
The latest high-performance MEMS acceleration sensor, AXO®, takes advantage of MEMS technologies*5 and a force-rebalance sensor architecture to achieve accuracies equivalent to those of conventional, analog crystal-based sensors, but in a much smaller, lighter and lower-cost package with a digital output. It features an accurate composite bias repeatability of 1mg even in challenging environmental flight conditions. The small SMD package and the digital output of the sensor will ease integration, help miniaturize, and reduce the cost of high-performance IMU and INS equipment.
The high-performance MEMS gyroscopic sensor GYPRO® features excellent bias stability even in harsh environments, and boasts ultra-low noise and low latency. It offers a digital output, smaller size and lower weight, and is a lower-cost alternative to traditional mechanical and fiber-optic gyros.
“High-precision, high-reliability inertial sensors are sure to play a critical role in emerging innovations like cargo drones and air taxis, and we are well-positioned to serve those opportunities,” added Gaff. “The repeatability and stability of our sensors and their continuous self-testing features enable our customers to build IMU and INS equipment for even safety-critical applications.”
TDK’s inertial sensors will continue to empower the advancement of technologies and growth of industries where higher precision and reliability are required, such as autonomous vehicles, railroads, aircraft, precision measuring instruments, robotics and industrial equipment.
AXO315 ® Accelerometer / GYPRO ® Gyroscope
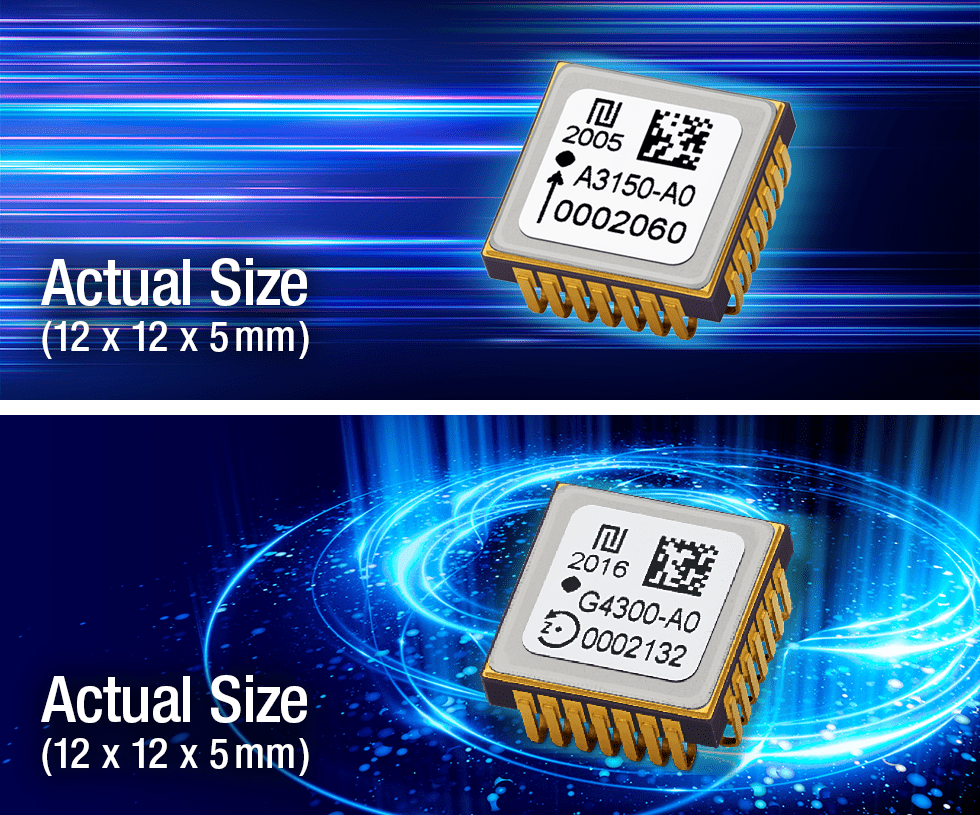
TDK’s accelerometers and gyroscopic sensors are amalgamations of advanced MEMS technologies. These high value-added digital MEMS inertial sensors are enabling the creation of new solutions for mobility and for the industrial IoT era. For more information, please visit our Product Center.
Terminology
- Dead reckoning: A method of computing the position of a vehicle using only onboard equipment.
- Avionics: Electronic equipment used for the flight of aircraft. The term is a portmanteau formed from the words “aviation” and “electronics.” They include autopilots, navigation systems and communication devices.
- Inertial Measurement Unit (IMU): An electronic device that measures and reports the acceleration, orientation, angular rates, and other gravitational forces of a vehicle based on measurements of inertia through accelerometers and gyroscopes.
- Inertial Navigation System (INS): A navigation device that uses a computer, motion sensors (accelerometers) and rotation sensors (gyroscopes) to continuously dead-reckon the position, orientation, and velocity (direction and speed of movement) of a moving object without the need for external references.
- MEMS (Micro-Electro-Mechanical Systems): Technology An extension of microfabrication technology for semiconductors that is used to integrate circuits, movable mechanisms and sensors on a silicon substrate and mass-produce them.
