【Sustainability and TDK】
What Are the Environmental Measures for Electronic Parts That Accelerate the Shift to a Circular Economy?
Economic and social activities based on mass production and consumption create a society based on mass waste and impede healthy material circulation. They are also closely related to various environmental problems such as climate change, depletion of natural resources, and destruction of biodiversity caused by large-scale resource extraction. The demand for resources, energy, and food, as well as the amount of waste generated, are becoming increasingly serious worldwide. Therefore, the global trend is to move from one-way economic and social activities to a circular economy that uses resources in a sustainable manner. TDK promotes product design and manufacturing processes aimed at a circular economy, in order to minimize the impact on the global environment throughout the product life cycle.
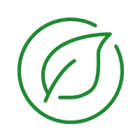